Wind Turbine Stall Modeling
NREL's stall modeling helps design wind turbines that can survive extreme weather, including rough seas offshore wind turbines must withstand.
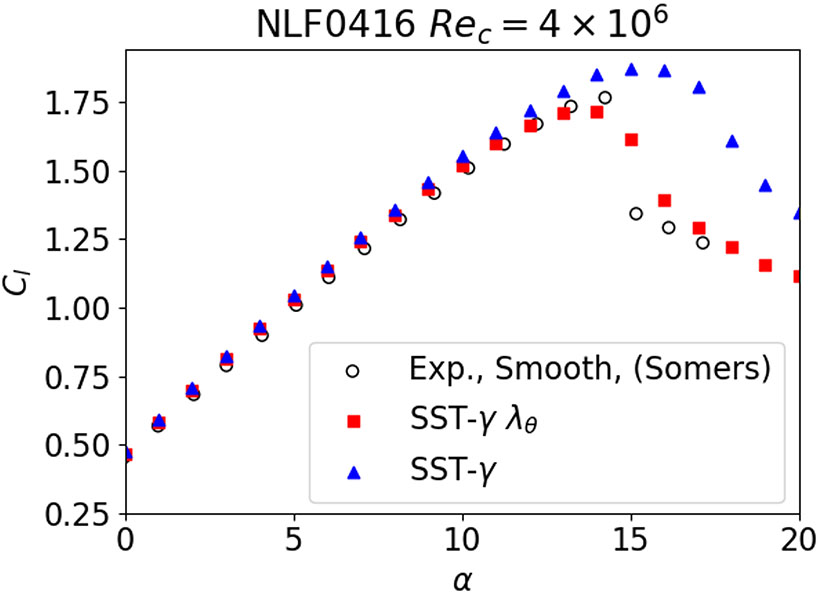
The turbulence (Reynolds-Averaged Navier Stokes) model detects regions of strong pressure gradients and augments the transport equation for eddy viscosity in these regions. It can greatly improve the prediction of separation, the phenomenon that causes wind turbine and aircraft stall.
When wind is misaligned with a wind turbine blade—e.g., due to gusty weather—the blade experiences a massive drop and power and increase in mechanical stress, a phenomenon known as stall. Existing computer simulation tools used to design and operate wind turbines struggle to reliably predict stall.
Publications
Improved Pressure-Gradient Sensor for the Prediction of Separation Onset in RANS models, arXiv (2024)
Development Team
NREL's wind turbine stall modeling development team includes Kevin Griffin, Bumseok Lee, Michael Sprague, and Ganesh Vijayakumar.
Contacts
Share
Last Updated June 5, 2025