Corrosion and Durability Research
NREL has customized apparatuses for materials synthesis processing, characterization, and testing. We evaluate corrosion and durability using our multiple high- and low-temperature materials durability research facilities. Read more on NREL's successes, projects, and publications on corrosion and durability.
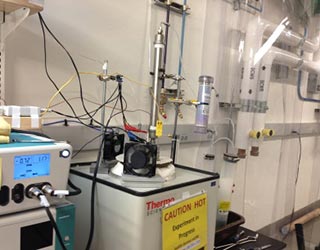
(a)
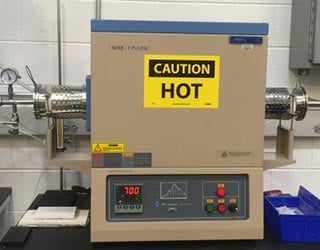
(b)
High-temperature corrosion: (a) High-temperature crucible furnace with controlled atmosphere electrochemical cell and instrumentation for corrosion evaluations. (b) High-temperature tube furnace with controlled atmosphere for weight-change corrosion evaluation.
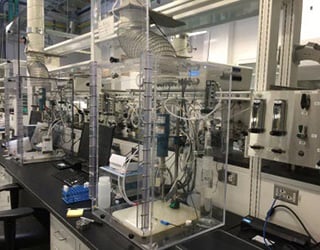
(a)
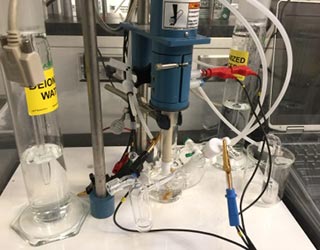
(b)
Low-temperature corrosion: (a) Electrochemical cells and instrumentation for low-temperature corrosion evaluations. (b) Rotating electrode to determine effect of mass transport on low-temperature corrosion.
The corrosion apparatuses are located in the Energy Systems Integrated Facility (ESIF), a state-of-the-art laboratory facility where we have full access to materials and components testing and characterization, in addition to a high-performance computing (HPC) system that can handle and analyze integrated data. The experimental and computational capabilities allow us to tackle scientific challenges covering the full range of energy systems.
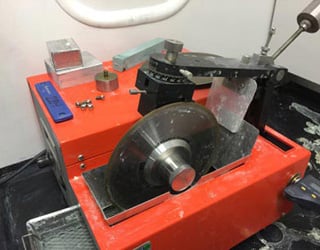
(a)
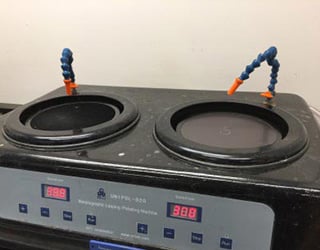
(b)
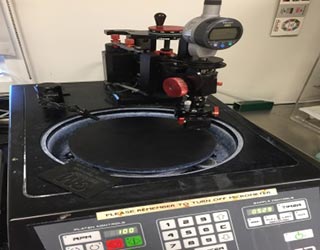
(c)
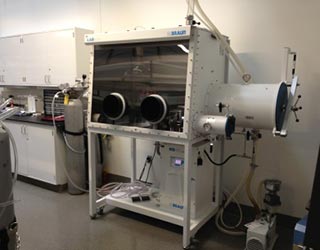
(d)
Sample preparation: (a) Low-speed diamond saw for sample cutting. (b) Grinder/polisher for sample preparation. (c) Automated polisher for sample preparation. (d) Glove-box to handle unstable samples.
NREL's corrosion/degradation evaluations focus on determining corrosion rates and mechanisms of systems. Our goal is to test corrosion mitigation approaches that we are developing to determine their efficacy.
We use electrochemical and conventional weight-change techniques. Controlled testing can be performed under a range of conditions, such as: different atmospheres, different temperatures (from room temperature up to 1,400°C), thermal cycling, and different fluids (molten salts, liquid metals, and aqueous solutions) and/or gasses.
Electrochemical reactions can be studied using galvanostat/potentiostat instruments with frequency-response analyzer.
Kinetic fundamentals of corrosion mechanisms are studied by several techniques, including cyclic voltammetry, linear polarization resistance, potentiodynamic polarization sweep, and electrochemical impedance spectroscopy.
Metallographic characterization of materials and chemical characterization of the materials and fluids are used before and after exposure.
Metallographic characterization includes metallographic preparation of samples for top-view and cross-section analysis. The preparation for characterization involves sectioning, encapsulation, grinding, polishing, and etching. We perform the metallography characterization using optical and electron microscopy instruments, X-ray diffraction (XRD), X-ray photoelectron spectroscopy (XPS), and energy-dispersive X-ray spectroscopy (EDS), among others.
Gas, dry, and wet-chemical instruments include gas and ion chromatographs, and inductively coupled plasma mass spectrometry (ICP-MS). These analyses help to fully understand which elements are depleted, plated, permeated, and/or concentrated in the material—and how they are—during processes.
Differential scanning calorimeters that can go up to 1,500°C with two furnaces (Pt and SiC) and an autosampler (DSC 404 F3) from Netzsch. The thermogravimetric analyzer can go up to 1,200°C (TGA/DSC1 Stare System from Mettler Toledo). The high-temperature test unit supplies/withdraws thermal energy from heat-transfer fluids at a 30-kW power rating. We also do XRD with several electron microscopes (TEM, SEM), among other state-of-the-art characterization tools.
Our staff has considerable expertise using the Peregrine-HPC system in ESIF for techno-economic analysis, thermodynamic and kinetic modeling, and process modeling and analysis. We can model degradation-predictable behavior using our materials computational and modeling staff.
Peregrine has about 11,520 Intel Xeon E5-2670 "SandyBridge" and 14,400 next-generation Intel Xeon "Ivy Bridge" cores, plus an additional 576 Intel Phi Intel Many Integrated Core (MIC) core co-processors with 60+ cores each. The nodes are connected using FDR Infiniband. Peregrine delivers a peak performance of 1 petaFLOPS. Peregrine runs the Linux Operating System and has a dedicated Lustre file system with about 1 petabyte of online storage and an initial capacity of 3 petabytes of mass storage capability.
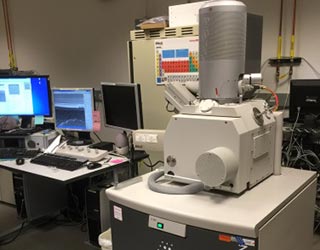
(a)
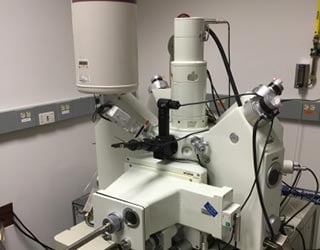
(b)
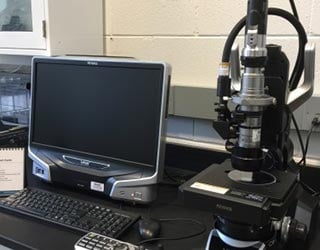
(c)
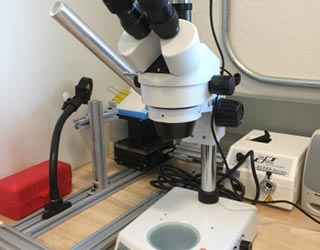
(d)
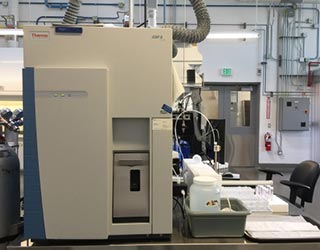
(e)
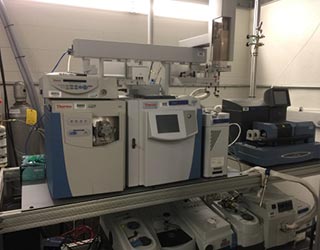
(f)
Sample characterization: (a) Field-emission scanning electron microscope (FESEM). (b) Scanning electron microscope (SEM). (c) Keyence digital 1,000X light microscope. (d) Stereo microscope. (e) Inductively couple plasma mass spectrometer (ICP-MS) for wet chemistry analysis of samples. (f) Thermogravimetric analyzer (TGA) on right and gass chromatograph (GC) for decomposition analysis of samples.
Share
Last Updated March 26, 2025