Your Renewable Energy Technology is Growing Old--What's Next?
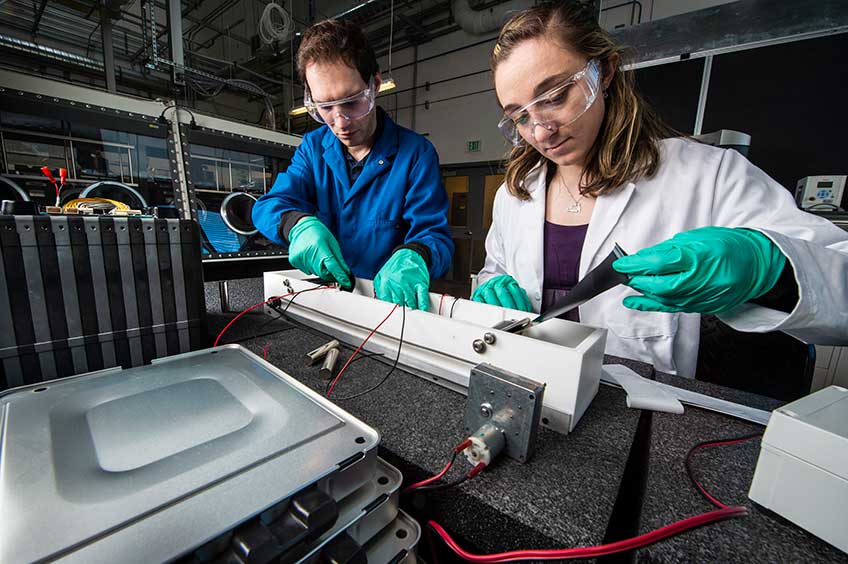
The cutting-edge research at the U.S. Department of Energy's (DOE's) National Renewable Energy Laboratory (NREL) will one day go to waste—but not into a landfill.
Every technology eventually runs into the end of its life. Photovoltaic (PV) panels and lithium-ion (Li-ion) batteries become less effective and need to be replaced. Researchers at NREL are making strides toward ensuring old technology can be more easily recycled.
"We're thinking about this broadly across many technologies, but PV is the one we've been thinking about the longest at the lab," said Garvin Heath, a senior scientist and member of the Resources and Sustainability Group in NREL's Strategic Energy Analysis Center.
While hundreds of millions of tons of trash continue to be dumped into American landfills annually, a growing percentage has been diverted to recycling centers since the first Earth Day in 1970. But these centers aren't set up for renewable energy technologies. NREL is looking to answer questions such as: "What methods should be used to recycle materials from PV panels and batteries used to power electric vehicles?" and "How can that be done economically?"
Globally, the amount of energy generated by PV has risen exponentially since the early 1990s, when it barely registered, to 512 gigawatts last year. The amount is expected to hit 4.5 terawatts in 2050. Lagging that increase will come a surfeit of PV panels past their prime. In 2050, the United States is projected to have 10 million metric tons of PV waste—half of what China's problem will be, according to a report co-authored by Heath. In addition to his work at NREL, Heath leads a task force on the sustainability issues of PV for the International Energy Agency.
Most solar panels today use silicon in converting sunlight into electricity and carry a 25-year warranty. More than 90% of a PV panel's weight comes from glass, plastic, and aluminum, which aren't hazardous waste. But the trace elements of silver, tin, and lead that are also part of the panels are considered hazardous, so ensuring proper disposal at end of life is important.
It's also important to recover the precious, critical, and hazardous materials in end-of-life panels. "If we can extract the materials, the potential value of those materials is considerable," Heath said.
A 2050 estimate projects that, in the United States, enough raw materials can be recovered to produce 2 billion new panels (the equivalent of 630 gigawatts) and puts the value of those materials at $15 billion. "Of course, if those materials go back into creating new modules, that's a nice circular loop," Heath said. "Not all those materials are going to be able to do that, but there's potential there."
One U.S. manufacturer, First Solar, unveiled a free PV recycling program in 2005. The company's panels differ from the more commonly used silicon panels in that they are made using cadmium telluride (CdTe), and cadmium ranks as one of the most toxic materials on the planet. First Solar recaptures about 95% of the CdTe, refines it, and then reuses it in a new solar panel through a recycling process they own and run at several facilities around the world.
A law that took effect last year across the European Union requires that at least 85% of waste from PV panels must be recovered, and 80% of that waste must be either recycled or reused. "This is just a start," said Michael Kempe, a senior scientist at NREL. "It essentially means that the frames and glass need to be recycled because that is where the mass is."
In the United States, only one state has decided what must be done with PV panels at the end of their life. In 2017 Washington approved a law requiring manufacturers to finance a takeback and recycling system at no cost to the owner. The law will take effect in 2021, at which time only PV manufacturers participating in a recycling plan will be allowed to sell their panels in the state.
Recycling PV panels will require that they first be collected and transported, which is an expensive process. Then the components must be separated, which is also expensive. The Electric Power Research Institute reports of hearing recyclers quoting prices between $10 and $30 a module just for processing. The costs are expected to come down as the amount of waste volume increases.
The price that owners of rooftop PV panels ultimately must pay will determine where that piece of technology winds up. "If they have to pay $25 to recycle it, it's going in a landfill," Kempe said. "But if they can take it to a recycling facility for free, that's where it will go. This is why it is so important for economical recycling processes to be developed and implemented."
Kempe, whose research focuses on ways to extend the lifespan of PV panels, said his goal is to see them last for 50 years. Manufacturers could make some changes to a PV panel so that it would be easier to recycle decades from now, but that's not likely to happen if it means sacrificing durability or performance. "That trumps ease of recycling," Kempe said.
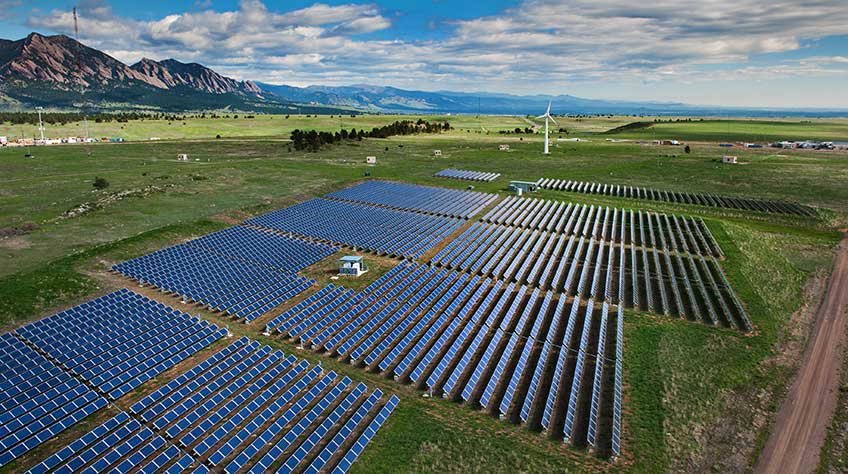
Battery Research Includes National Prize for Recycling Effort
A new area of research at NREL involves the ease of recycling Li-ion batteries. Those batteries are expected to become ubiquitous as more electric vehicles hit the road. Electric vehicles make up only about 1% of new car sales in the United States, but that is expected to reach 22% in 2025.
To address issues related to recycling Li-ion batteries, DOE in February unveiled the ReCell Center, a collaboration between NREL, Argonne National Laboratory, Oak Ridge National Laboratory, and several universities. NREL's role in ReCell calls for coming up with a new design for Li-ion batteries, one that will be easy to recycle, said Ahmad Pesaran, the laboratory's energy storage chief engineer. "Right now, the way batteries are put together, it's welded. Everything's tightly together. It's not conducive to pulling part. You have to shred everything at the same time. This creates a lot of waste."
Total battery waste is forecast to reach as much as 170,000 tons a year by 2020, and currently only a handful of U.S. companies are set up to reclaim and recycle the materials used in Li-ion batteries: lithium, cobalt, manganese, nickel, and graphite. But by recycling and reusing certain high-value elements—notably lithium and cobalt—manufacturers would be able to lower their costs and stave off potential shortages of those materials.
"The good thing is we already have these batteries here in the United States, so it's sort of like a virtual mine of cobalt," said Ahmad Mayyas, an NREL engineer who has written about the case for recycling Li-ion automotive batteries. "So why should these batteries go to the landfill?"
Laws are already in place across the country to keep lead acid batteries out of landfills, and according to the Environmental Protection Agency, about 99% are recycled. The lead is then used to make new batteries.
The issue of recycling Li-ion batteries is more complicated, partly because no laws exist forbidding the dumping of this spent technology. The more diverse materials used in Li-ion batteries requires careful sorting. Then there's the potential for fires if the batteries are improperly handled. "There have been fires in waste management facilities because people throw their cellphone and laptop batteries in the waste," Pesaran said.
Plus, the U.S. Department of Transportation considers Li-ion batteries hazardous to transport. "It doesn't matter if you have the best recycling approach if you cannot collect them and send them to the recycling facilities cost-effectively and safely," Pesaran said.
To help address these challenges, NREL is administering DOE's $5.5 million Lithium-Ion Battery Recycling Prize, an upcoming competition intended to find the best ways to profitably capture 90% of spent or discarded Li-ion batteries by collecting, sorting, and transporting them to recycling facilities so that the materials can be reused. Registration for the challenge closes July 31.
Research Could Make Composite Materials Recyclable
Another notable NREL project involves converting a single-use plastic bottle into something more valuable and, in the process, creating an economic incentive to deter discarding. Only about 29% of plastic bottles in the United States are recycled annually, according to the American Chemistry Council. That leaves a lot of plastic tossed aside.
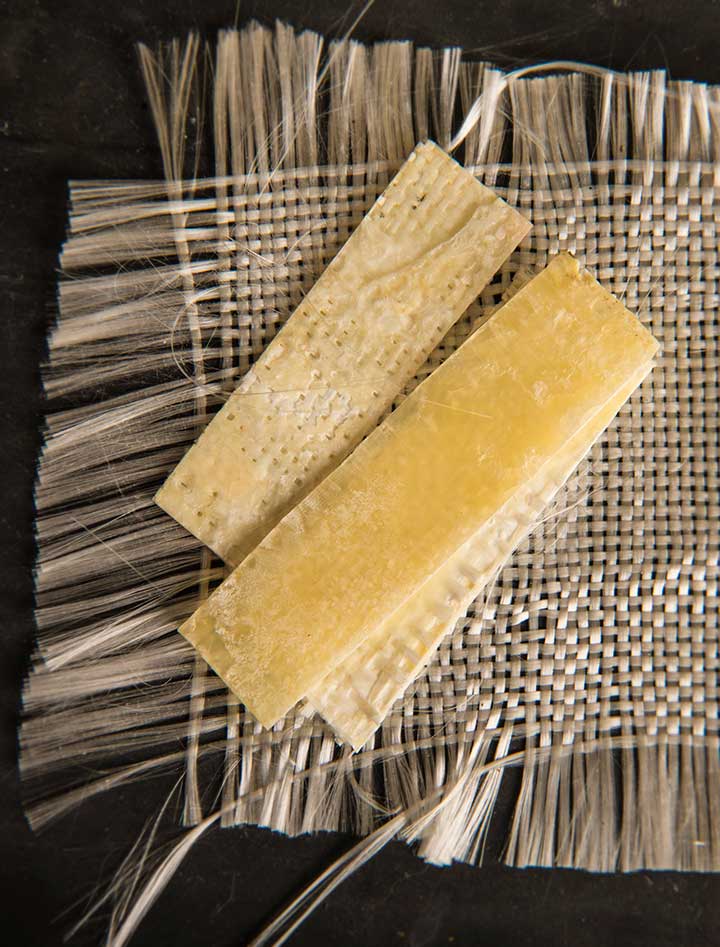
Gregg Beckham, a senior research fellow at NREL, and his colleagues developed a chemical process to combine the plastic commonly used for water bottles, polyethylene terephthalate (PET), with bio-based compounds. The result is a composite material that's noticeably stronger than the original plastic and can be used to make everything from snowboards to wind turbine blades.
"A water bottle you use from minutes to hours," Beckham said. "A composite material you typically use from years to decades."
Recyclers shred PET into flakes, which can then be reconstituted into other materials such as carpets and polyester clothing. But the going rate for reclaimed PET is small, at about 51 cents a pound. Turning that PET into a composite increases its worth. "The inherent value, the selling price, of the composite material will be much greater," Beckham said, estimating the number at $2.60 a pound.
When that composite material nears the end of its lifespan, however, another issue emerges. Composites can't be easily recycled, nor can they be broken down into component parts for reuse. NREL researchers want to change that.
"We're working on ways to basically put Trojan horses into a composite such that during its lifetime as a wind turbine or a snowboard, it's fine," Beckham said. "It will do its thing and will look and feel and act exactly like those materials. But at the end of its life you could dump it into acid or dump it into base or heat it up well beyond its operational temperature and then make it into something that can flow again and you can recycle it into, for example, another composite."
Derek Berry, a senior engineer with NREL's National Wind Technology Center, faces the problem of what to do with composite blades from wind turbines that have outlived their usefulness. The blades are designed to last for 20 years, but turbine operators can swap them out for newer, better models capable of generating more energy.
"The amount of new energy production annually is often worth the cost of scrapping the old blades and installing new ones," Berry said. "All of a sudden on a given wind farm you might have hundreds of blades taken down and what do you do with those blades?"
One forecast estimates there could be as much as 705,000 tons of discarded wind turbine blades in the United States by 2030. The blades often wind up at the landfill. As for recycling, that typically involves chopping them into small pieces and using that to shore up a concrete mix, for example.
Changing the chemical makeup of a blade could lead to producing ones that can be recycled and their materials reused, NREL researchers have predicted. The current process to make a blade uses fiberglass or carbon fiber mixed with a thermoset resin, which is heated to form a fiber-reinforced composite. "That is irreversible," Berry said. "You can heat that up all you want; it's not going to melt. You can burn it, but you get very little out of it. It's an irreversible process and therefore it's very, very difficult to recycle."
NREL researchers are experimenting with a thermoplastic resin system, which cures at room temperature. The result is a blade that's potentially less expensive to manufacture and capable of being recycled. "You can apply a certain amount of heat, melt it down, turn it back to liquid, and use the resin system again," Berry said.
NREL is preparing to validate how a 13-meter wind turbine blade made using the new thermoplastic system and compare the results against a baseline blade manufactured with traditional thermoset resin. The blades were both made from the same mold, which will provide a nearly exact comparison. "This will be a huge step for us," Berry said. "If everything goes well, the next step is to work with industry partners to help them commercialize the material."
Last Updated May 28, 2025