NREL Discusses Circular Economy With High-Profile Partners in Fourth Partner Forum
Patagonia, Kraft Heinz, World Wildlife Fund, Arkema Inc., GE Subsidiary LM Wind Power Explore Barriers, Solutions for Economy of Tomorrow
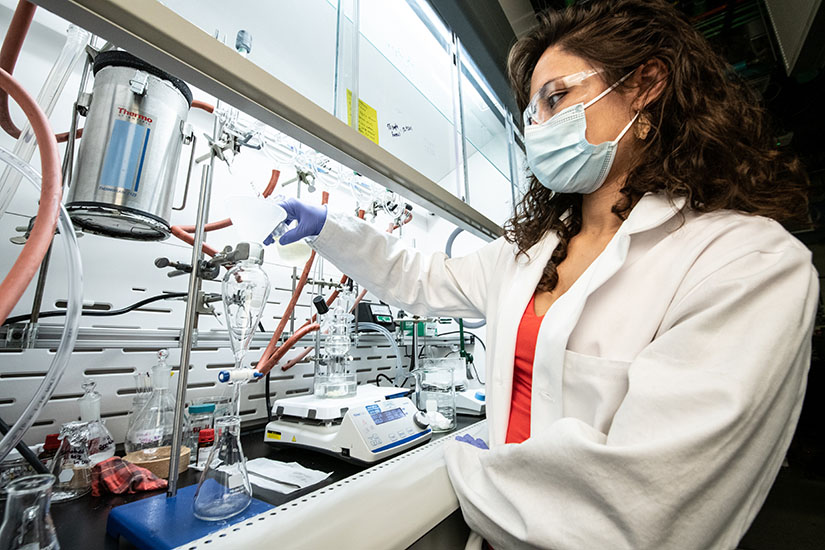
Barely a month into the new year and only weeks into the new administration, renewable energy has emerged with a deliberate thrust forward. Front and center, the National Renewable Energy Laboratory (NREL) stands ready, poised to build upon its nearly 45 years of expertise and accelerate its longstanding and unwavering mission to advance the science and engineering of energy efficiency, sustainable transportation, and renewable power technologies.
On February 3, having wasted no time, NREL used its fourth annual Partner Forum—focused on solutions to enable a circular economy for energy materials—to showcase its stable of leading experts and open its virtual doors to partners, extending invitations to companies, large and small, from around the world to engage in a collaborative effort to design a future replete with renewable energy solutions to the energy challenges of today.
Early on the morning of the event, NREL Associate Laboratory Director for Innovation, Partnering, and Outreach Bill Farris turned on his webcam, unmuted his microphone, and welcomed more than 300 invited viewers, panelists, and speakers to the four-hour virtual event.
“NREL's purpose is to explore and develop research opportunities that improve and advance energy solutions for all,” he said. “In the past four decades, we have also shown that acting as a convenor and collaborator can achieve a multiplier effect across the energy landscape is part of our DNA. We know that we can do much more together than on our own, and we are steadfast in constantly finding new mechanisms and systems to make meaningful partnerships and collaborations happen.”
In succession, the U.S. Department of Energy (DOE) Deputy Assistant Secretary, Operations (acting) and Golden Field Office Director Derek Passarelli and NREL Director Martin Keller focused participants on the goal, the tasks at hand, and foreshadowed the path to a sustainable future.
Before Keller introduced NREL's research strategy through the strategic pillars of integrated energy pathways, electrons to molecules, and the epicenter of the Partner Forum, circular economy, he looked ahead to energy demands of the future and highlighted a few key mega trends that must be addressed now. The growth of energy use in the developing world will far outpace growth elsewhere. Global renewable power demand will grow. Urbanization trends will dominate new infrastructure growth. Electrification and electric vehicle adoption will increase dramatically. Demand for high-density liquid fuels will expand, and digitization, data, decentralization will be strong drivers of energy transition.
“We need new ways of creating, delivering, and securing power,” he said. “By collaborating with these partners, we are conducting research to discover answers to a host of questions about significant energy issues.”
Erin Simon, head of plastic waste and business at World Wildlife Fund, accepted a handoff from Keller and dove headfirst into the world's and, more specifically, the United States' struggle to right a listing ship of plastic waste pollution through concerted efforts to reduce, reuse, recycle, and upcycle plastics.
“Americans account for 5% of the world's population, but we create half of the world's solid waste, and 72% of that ends up in landfills,” she said. “The U.S. really represents a big opportunity for recycling. There's a big gap between how much plastic companies are putting into the system and how much is being recycled.”
In a business-as-usual scenario, Simon said, by 2040, we will have produced twice the amount of plastic, three times as much will end up in oceans, and accumulations in the oceans will be four times what they are now.
“Plastic has no place in nature,” Simon repeated throughout her presentation. “It represents a mismanagement of resources, and we need to fix the broken and complex system that has taken us to where we are today. We're leading the charge to reimagine how we design, dispose of, and replace the plastic we rely on.”
Partnerships, Honoring Commitments, and Consumer Education Empower the Economy of Tomorrow
More than 12 years ago, at the start of NREL's current management contract with the Alliance for Sustainable Energy LLC (Alliance), NREL accelerated its partnership outreach. During that period, the laboratory has generated partnership projects totaling more than $1 billion in research-and-development contract value, and in fiscal year 2020, NREL delivered a single-year milestone, booking $102 million in new partnership agreements. That activity continues to grow, and in its unending quest to transform energy through innovation, NREL maintains about 900 active partnership agreements with more than 587 distinct partners.
As the forum progressed, the need for partnerships developed as a clear and steady theme. Almost every speaker implied or outright stated the need for partnerships and collective action to generate impact. Simon, in her keynote, said companies need to be successful in meeting their commitments in order for World Wildlife Fund to reach its goal of having no plastic in nature.
As part of the BOTTLE™ and Plastics for the Future panel, Linda Roman, head of packaging growth and technology at Kraft Heinz, said, “Globally, we aim to make 100% of our packaging reusable, recyclable, or compostable by 2025. We want to increase the use of recycled content and decrease the volume of packaging. We recognize we can't do it alone. We have to have partnerships in what we do.”
BOTTLE is an acronym for a consortium officially launched in October 2020, which breaks down to Bio-Optimized Technologies to keep Thermoplastics out of Landfills and the Environment (BOTTLE). The consortium, led by NREL researcher Gregg Beckham, in partnership with companies like Roman's, works to break down materials that are in some cases very complex.
BOTTLE is not grabbing at the low-hanging fruit either. Bob Baldwin, a principal scientist in NREL's National Bioenergy Center who works on the business development side of BOTTLE, said he and Ron Schoon, the panel's moderator and the business development lead for BOTTLE, have reached out to about 100 companies so far, looking to engage in order to help solve difficult problems.
“We tell them, give us your tough problems. We want to work on things that really don't have a technology solution today, and that resonates strongly with companies like Kraft-Heinz that have some really tough challenges,” Baldwin said.
BOTTLE asked for difficult problems and received them. What may appear to be simple materials to the naked eye, such as a container label or rock-climbing attire, may in fact be very complex material. Natalie Banakis from Patagonia Inc., another of the panelists, discussed some of the difficulties associated with creating high-performance materials while sticking to a mission-driven business with a mission to “save our home planet.”
“We're able to utilize bottles for our polyesters, and we've found resources for our nylons as well. For us, it's the challenge of these technical pieces and what to do with them at the end of life,” Banakis said. “Textiles are extremely difficult to recycle using traditional methods. We need partnerships and collaborations to be successful.”
That is where BOTTLE comes in and can engage Beckham's research “dream team” of partnering national laboratories and universities, each bringing a specific specialty to manufacture holistic solutions to these multifaceted problems.
“Some materials have been so incredibly highly engineered, the solution is really specific to that material and that packaging and really nobody else,” Baldwin said.
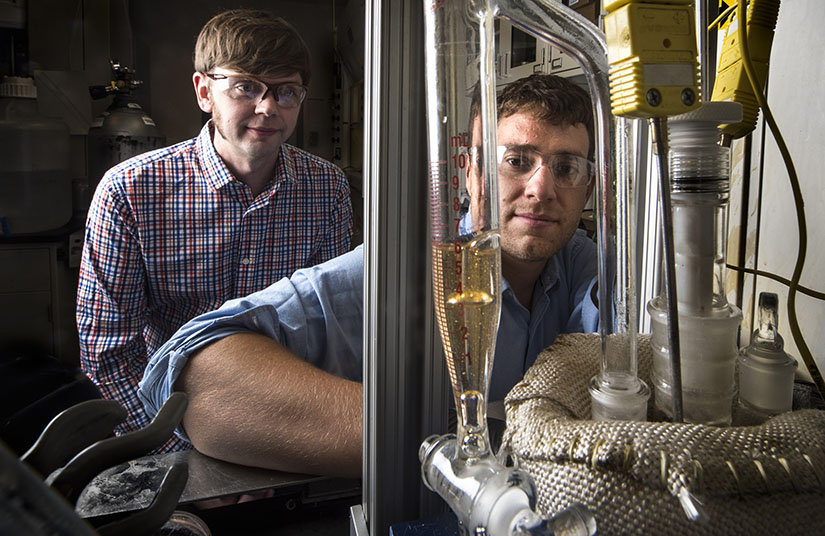
Both Kraft Heinz and Patagonia said they recognize the need for consumer education and maintain programs designed to help consumers understand what to do with their products at end of life.
“We leverage and recognize the value of consumer communication. We can make the best reusable package in the world, but if the consumer doesn't know what to do with it, it doesn't happen,” Roman said.
For years, Patagonia has been buying back its materials to keep them out of landfills, but as Banakis noted, “All of these end-of-life solutions rely on our customers knowing what to do with that product and having a desire to do the right thing. It's up to our customers, so we try to educate them, but also form partnerships and collaborations.”
Beckham said BOTTLE has been able to leverage tools that have been foundationally put in place by DOE's Bioenergy Technologies (BETO) and Advanced Manufacturing (AMO) offices.
“We think we can make some significant contributions with this really wonderful team that has been put in place as the BOTTLE consortium,” he added.
Acting AMO Director Valri Lightner said AMO conducts analysis and NREL is a big partner in that. She specifically referenced the NREL-developed Materials Flow through Industry modeling tool, saying it informs the work we do in circular economy.
During the panel sessions introduction, acting BETO Director Valerie Reed really simplified the problem and the call to action, saying, “Plastics are designed to be difficult to degrade. That's what made them valuable in the first place. Recycling them is difficult and costly, but the technologies that are funded through the BETO in deconstruction and upgrading can be applied to this problem, and we envision we'll be able to tackle these with the projects we're working here and with AMO.”
A Circular Economy Means Better Design for Tomorrow, but Also Responsible Action With the Products of Today
The afternoon panel, moderated by NREL senior research fellow Bob Allen, covered Composites and Energy Materials in the Application Space and included comment from NREL senior wind technology engineer Derek Berry, technical development manager at Arkema Inc. Dana Swan, and product life cycle leader at LM Wind Power Katelyn Huber.
During this panel emerged a theme that has long been central to the transformation of energy to a renewable environment, which is especially relevant to wind turbine blades: the need to slay the two-headed monster of recycling materials already in circulation and designing materials going forward with end of life in mind.
“What we're experiencing is a wave of end of life for hundreds of thousands of installed wind turbine blades. If we look out to the year 2050, the composite waste from wind turbine blades alone coming off turbines is going to constitute 50 million metric tons,” Berry said.
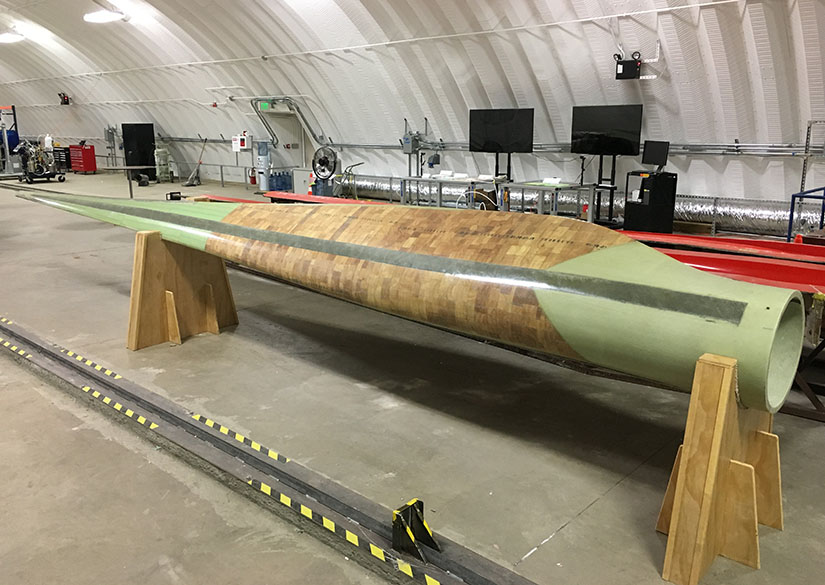
Recycling a wind turbine blade, however, is not as simple as dragging it out to the company recycle bin. At one point during the panel, Huber created a momentary pause when she keyed up and stated, “Blades are 100% recyclable already, contrary to public opinion. The issue is they aren't 100% recycled in practice.”
What she was referring to is the practice of chopping up wind blades and using the pieces in cement, for instance. Some large companies with strong interests in managing their environmental footprints, such as longtime NREL partner General Electric, parent company of LM Wind Power since 2017, are able to commit to such practices, but ultimately, economic factors are preventing other companies from easily taking those steps.
“You can chop up every single blade and use the aggregate and mix it in with concrete or even use it as some filler in other applications, but that's not true recycling,” Berry said. “You can do that, but what it comes down to is it's not economically feasible. Nobody is going to do that with all their blades. They may just allow them to sit in a field until another solution comes along. Our approach is to find solutions that increase the value of the recovered material and make it financially viable so it doesn't cost more than landfilling options.”
Turning to the question of how best to design future turbine blades with end of life in mind, Swan toured participants through the details and value of the Arkema resin Elium—a game-changer in wind turbine technology. Berry detailed why Elium has been so beneficial and how it can both enable more cost-effective blade recycling and improve basic blade design.
“Right now, if we build an epoxy blade, we have to use heated molds that can cost many millions of dollars per mold set,” he said. “If we produce blades with Elium, we can do it at room temperature. In addition, we have the ability, with Elium, to thermally weld blade components together.”
Elium can save manufacturers time, energy, and capital expenses. They do not need to buy the oven used to post-cure blades. There are tradeoffs, Berry said. Some of the up-front cost may be a bit higher, but it can lead to less capital investment, reduced labor, and could eventually result in lower-cost wind blades. An NREL study suggests that blades using the Elium resin system could be as much as 5% cheaper.
Berry said six years ago, from discussions he had with many manufacturers, recyclability of blades was often not a priority, or if it was important to a company, the contact would tell him there were many higher priorities. Today, Berry said, for those same companies, recycling is the top priority, and they are very interested in solutions. In addition, the ability of Elium to potentially enable thermal welding may be leading companies to this new technology as much as anything else.
“Turbine OEMs and blade manufacturers come back and say, ‘We really like the idea of recyclable blades, but it is a difficult proposition to pay more for it,'” he said. “If you can demonstrate to us that you can thermally weld blade components and solve many of our challenges with the bonding process, that kind of enabling can drive this innovative technology forward.”
One truth is painfully apparent, and Bob Marlay, DOE Wind Energy Technologies Office director, called it out directly in the afternoon panel introduction. “If you're really going to get to 2035, with full decarbonization, almost every energy technology plays a role, but in the scenarios, there's one thing that just jumps off the page, and that's that wind energy has to grow something like five times,” he said. “For us, that means five times. We have to go from 110 MW to 550 MW. Some say even that is underachieving the goal for wind.”
During the morning panel introductions, NREL Associate Laboratory Director for Bioenergy Science and Technology Adam Bratis said one thing NREL is really focused on from a circular economy perspective is building end-of-life and circular-economy considerations into the clean energy technologies it is developing. He then posed the circular economy question: “How do we build these into our technologies without compromising performance—how do we design tomorrow's plastics with not just reliability and cost in mind, but with end of life in mind as well?”
From NREL Partner Forum discussions, it is clear the final answers, whatever they may be, necessitate partnerships and collaborations; attention to solutions for past, present, and future environmental technologies and materials; consumer education; and organizational and individual desire to do the right thing. The time is now. And with the capabilities, experience, resources, and desire to partner on real-time solutions to worldwide energy challenges, the place is distinctly NREL.
Learn more about partnering with NREL.
Last Updated May 28, 2025