CABLE Conductor Manufacturing Prize Announces Stage 1 Winners
Prize Rewards Breakthrough Concepts for Affordable and Manufacturable Conductivity-Enhanced, Next-Generation Materials
To transition to a clean energy economy, we must rewire the future of electricity. And the U.S. Department of Energy (DOE) is asking researchers and innovators to do just that.
Today, DOE’s Office of Energy Efficiency and Renewable Energy announced 10 teams as Stage 1 winners of the Conductivity-enhanced materials for Affordable, Breakthrough Leapfrog Electric and thermal applications (CABLE) Conductor Manufacturing Prize, run by DOE’s Advanced Manufacturing Office and administered by the National Renewable Energy Laboratory. During this $4.5 million, three-stage prize, teams compete to design and make conductivity-enhanced materials and propose ways to apply these materials to help upgrade and expand aging electric and transportation infrastructures in the United States. Their novel designs could help lower costs and improve grid performance—including during extreme weather events.
For more than 100 years, copper powered everything from lightbulbs and telegraphs to the first telephones. But engineers have been able to increase the conductivity of copper wires by only a few percentage points since 1913. The same is true for aluminum, which runs through most overhead power lines, and although it is lighter and costs less than copper, it is also less conductive. To meet today’s U.S. electricity demands and help the country achieve the Biden administration’s goal of a carbon-pollution-free grid by 2035, new materials will need to beat that historical rate of improvement significantly—with at least a 10% conductivity increase without a corresponding cost increase.
Even a 10% increase in electrical conductivity is a big leap, and it is risky too—likely requiring new scientific advancements to create affordable improvements. The CABLE Prize provides funding and technical assistance to help alleviate that risk and encourage teams from diverse backgrounds and perspectives to chase creative, new ideas that can enable U.S. manufacturers of cables and electrical equipment to leapfrog to next-generation conductive materials.
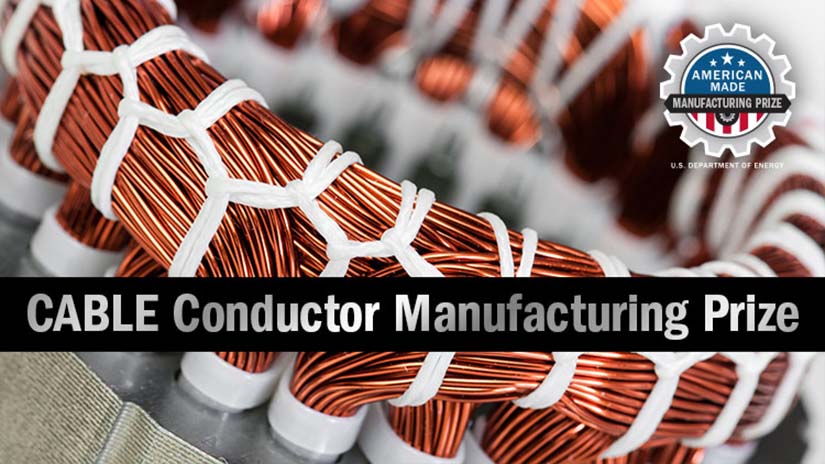
In Stage 1, which launched in March 2021 and concluded in August 2021, teams submitted breakthrough concepts for more conductive (and affordable) materials that could be used for both electrical and thermal (heat-based) energy applications. Now, with Stage 1 complete, 10 teams and their early-stage concepts have each earned a $25,000 cash prize and a stipend to support third-party testing in Stage 2, when they must manufacture a microscale sample of their material.
- Based in Houston, Texas, the Clean Carbon Conductors team, with members from Rice University and DexMat Co, is designing enhanced-conductivity carbon nanotubes (CNTs) by improving fiber quality, alignment, packing density, and by electrochemically doping the CNTs.
- Team NAECO from Peachtree City, Georgia, submitted their entry for Conductivity Enhanced Alloys with Nano Additives, which involves first mixing copper with trace amounts of additives before combining it with graphene using solid phase processing.
- MetalKraft Technologies in Athens, Ohio, with members from Lehigh University, is also using solid phase processing to create Copper-Graphene Ultra Wire with small amounts of commercially available low-defect crystalline graphene.
- In Niskayuna, New York, the GE Research team will use Electron Beam Melting Additive Manufacturing of Ultra-Conductive Components to fabricate a nano-carbon-metal composite from copper and low-cost graphite powder, carbon black, or possibly higher-cost nanostructured carbon.
- VT Materials in Blacksburg, Virginia, submitted their entry for an Enhanced Conductivity Overhead (ECO) Wire made from aluminum (potentially from recycled wires), graphene, and other nano additives.
- Based in Butte, Montana, the 59701 Nano Innovations team is designing a Highly Conductive CNT-Composite Cable made from CNTs that are manufactured from carbon dioxide and small amounts of metal, such as copper from the local mine.
- For their Intercalation Compounds of Carbon Fibers (ICF) project, the University of Texas at Austin team will create a high-conductivity carbon fiber, which competes with CNTs in conductivity, by alternating layers of carbon fiber with transition metal chlorides.
- The SuperWire team in Burlington, Massachusetts, proposed A Manufacturing Strategy for CNT Power Cables to create a lightweight, high-strength, braided CNT-metal-composite cable by adding either copper or aluminum.
- The Super Cool Conductor from Selva Research Group in Houston, Texas, is making a rare-earth, high-temperature superconductor that could be manufactured at half the cost of copper and cooled with liquid nitrogen or cryocooling for applications such as long-duration electric storage.
- In Ashland, Massachusetts, the NanoAL Lightning team is creating Ultra-High-Strength/Highly Conductive Aluminum Alloys using traditional manufacturing equipment and specialized nano processes to replace steel cores in overhead power lines.
“For the country to reach a net-zero-carbon economy,” said Matt Ringer, the National Renewable Energy Laboratory’s Advanced Manufacturing Office laboratory program manager, “we need new, cutting-edge materials to move electricity from renewable technologies to the grid, electric cars, trains, and planes, motors, smart phones, and more.”
Recent advances in metallurgy (the science of metals) and nanoscience (the science of the atomically small) inspire the CABLE Prize-winning teams. For example, the 2004 discovery of CNTs, which are about 100 times thinner than a strand of human hair, revealed one of the toughest known materials, which could already conduct electricity better than copper at the nanoscale. CABLE Prize participants are also exploring the potential for other promising materials like brass, aluminum, and magnesium.
“It’s possible to increase the conductivity of copper and aluminum or discover entirely new materials that are both affordable and more conductive,” Ringer said. “Advances in nanoscience and metallurgy have shown us the path. We need to follow it.”
The competition will heat up in Stage 2, when teams take their materials from concept to reality, producing at least 1 gram for evaluation by CABLE Prize-approved testing labs. Competitors will also prepare preliminary plans to scale-up and manufacture their materials.
Stage 2 is not limited to only Stage 1 winners. All Stage 1 entries were top quality, and the selection process was highly competitive. The prize administration team encourages competitors who were not selected in Stage 1 to continue to refine their concept based on judges’ feedback and compete in Stage 2 of the competition.
New competitors can also join Stage 2 of the prize to compete for a $200,000 cash award, and a $100,000 noncash voucher to support work with one of DOE’s national laboratories or other American-Made Challenge Network providers to obtain testing services, scientific and technical assistance, and conductor assessments. Stage 1 winners received a testing stipend, but other teams must self-fund the required electrical conductivity testing at an approved testing facility.
Only competitors who win Stage 2 will move on to the third and final stage of the competition, wherein they will manufacture a larger sample of their conductivity-enhanced materials and develop plans to commercialize their designs. Up to four winning teams will split a total prize pool of at least $2 million in Stage 3.
The CABLE Prize Stage 1 winners were announced today in celebration of National Nanotechnology Day (observed). Many competitors are using nanotechnology to develop and manufacture new, affordable conductivity-enhanced materials. Watch the Nanotechnology for Energy Efficiency 101 video to explore how nanotechnology can improve energy efficiency.
Learn more about the CABLE Conductor Manufacturing Prize and sign up for updates on how to compete in Stage 2 of the prize.
Last Updated May 28, 2025