Q&A With Bob Allen: Cooking Up the Right Ingredients for a Circular Economy
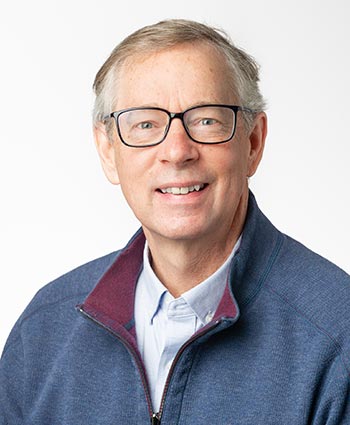
NREL Senior Research Fellow Bob Allen
This is the first in series of articles profiling NREL researchers whose work is helping build a circular economy to extend the lifespan of materials, components, and products, while reducing waste, conserving resources, and boosting efficiency. Ultimately, this approach will make it possible to manufacture goods that use less raw material and energy, last longer, and stay out of landfills.
NREL Senior Research Fellow Bob Allen shared his thoughts on how innovations in upcycling sustainable polymers and composites can contribute to the circular economy. He joined the laboratory's Bioenergy Science and Technology team after 35 years as an industrial polymer chemist and research leader at IBM's Almaden Research Center.
How does NREL's polymer science research contribute to the circular economy, with efforts to make manufacturing cleaner and more efficient, reduce waste and pollution, and upcycle recovered materials?
I like to think of designing new materials in terms of cooking. If you get into the details, with seemingly small changes you can make a tremendous difference in not just the taste of the food but the entire experience of a meal—or the ultimate performance of materials.
Traditionally we've had one basket of ingredients to make plastics (or polymers), and that basket has been filled with petroleum-based chemicals. Maybe think of these as comfort food, like mashed potatoes and gravy. That basket still exists, but we're trying to augment it with other healthy, more sustainable ingredients.
The second basket contains new materials derived from biomass that might lead to tremendous benefits and a much lighter carbon footprint. These are closer to ingredients you'd find in an organic grocery. And then the third basket holds new building blocks that we create by deconstructing and upcycling today's plastics, or leftovers.
If you take these three sets of ingredients, you can cook up all kinds of exciting new materials that reduce the energy use and waste typically associated with plastics manufacturing.
Why is plastic upcycling important to U.S. efforts to reduce climate-harming emissions, pollution, and energy use?
The 900 billion pounds of polymer plastic materials manufactured globally each year is a staggering amount. Less than 10% is currently recycled.
At the same time, it's amazing to realize about 6% of all energy consumption is used for this global manufacturing of petrochemical-based plastics. If we could substantially reduce the use of fossil energy to build new plastics, that would obviously be extremely beneficial.
Instead of using fossil energy to build a new mountain of plastics next year, wouldn't it be great if we could reclaim a substantial portion of that energy and waste material? Right now, the research we're working on at NREL is exploring more efficient processes to essentially reuse existing polymers and also to build new high-performance plastics that will be easily recycled.
What do you see as the biggest scientific and marketplace challenges in greening these processes and materials?
We all use textiles in the form of clothing and carpeting, and these are extremely challenging to upcycle at the end of their life. Some of the biggest hurdles have been the purity of materials and the economics.
First of all, they have a rather short life, especially when you think about things like fast fashion or athletic gear that gets heavy wear. And it's very complicated because these objects, unlike a Pepsi bottle, are multi-material, heavily dyed, with all sorts of different polymers in one product.
If you're trying to upcycle materials, the process can't be too expensive. In today's market, the value of plastic waste is very low. That means we lose a lot of plastic to landfills, or it ends up polluting the environment in other ways.
Plus, the output of this process has to be 99-plus-percent pure to create materials deemed worthy of upcycling. But all kinds of odds and ends show up in plastic recycling plants.
Not too long ago, we were processing some waste from a curbside pickup, and we thought we spotted a dead rat in there. Turned out it was a mannequin head. You never know what kinds of weird things you'll find.
How would you ever conceive of upcycling the crazy mix of materials you find in recycling bins? That's why our NREL team is working to develop new processes.
One path forward: selective digestion. We are getting sophisticated enough with catalysts (biocatalysts and thermal catalysts) that we can target one type of polymer—polyester for example—and selectively break it down. The rest of the odds and ends are essentially ignored by the deconstruction chemistry. In this way, pure monomer building blocks come out downstream.
What is the focus of your NREL team's research?
Wouldn't it be nice to build new materials that have essentially two design elements? Number one, designed for tremendous performance. But also designed for very easy deconstruction and upcycling at the end of that product's use or life. That's our big focus.
We're also applying the VolCat (volatile catalyst) process I developed at IBM to upcycle plastic waste. VolCat is one form of selective digestion we discussed earlier. DOE recently awarded NREL and IBM funding to evaluate the use of VolCat-like processes with textiles. By devising, optimizing, and scaling deconstruction and upcycling processes, we're hoping to bring the circular economy to the textile industry.
Our team is being joined by performance apparel maker Under Armour and textile manufacturer Milliken.
Milliken deeply understands polymer materials and various formulation additives that are required to make high-performance fibers in textiles. They will be instrumental in helping us understand how the additives and different polymer materials play into the deconstruction process.
With Under Armour, we'll be able to use some of their high-performance fabrics as upcycling feedstock for the VolCat process. This will help us see how changes in the material mix influence the process economics and the quality of the output from these processes.
Eventually, what else could this upcycled material be turned into?
It might be used for making all kinds of new products. Yes, you could use it for new
textiles. Or, depending on how it meets requirements for food grade applications,
for new PET (polyethylene terephthalate) plastic containers.
But it could also be used to create completely new items, industrial components for
renewable energy in addition to consumer products. For example, it could be used in
next-generation wind turbine blades.
Can you describe the VolCat process?
Polymerization is the chemistry by which you transform monomers (or small molecule building blocks) into polymers, gigantic molecules that are typically little monomer units strung together. Depolymerization is the reverse process of breaking these gigantic molecules back down into monomers.
Originally, back at IBM, we were really focused on one thing: How quickly can you digest mixed plastic waste down to the monomer?
We quickly realized that the original catalyst we'd landed on for depolymerization was fast but expensive, and economics are really important if you're trying to upcycle something. Plus, you need to have catalysts that are only active enough that they can perform what I call selective digestion—go after one component and pretty much ignore all the other things.
An even a bigger problem was finding a cost-effective way to remove the last traces of that fast catalyst from the monomer that came out. We didn't want to end up with PET that was bright yellow or brown, or with other characteristics that would make it impossible to use in fabricating a range of new products.
That led us to invent VolCat using a volatile catalyst with a blend of chemicals, atmospheric pressure, and heat to quickly and affordably process unwashed, unsorted waste plastic. It also allows us to completely recover and reuse the catalyst. That makes it a completely circular process, which helps the economics, but the quality of the output is high due in part to the high selectivity of the catalyst.
What unique capabilities does the NREL team bring to establishing a robust circular economy?
NREL has put together a very diverse team of chemists, biologists, and chemical engineers with a healthy dose of analysis and computation. With this interdisciplinary approach, we're able to look holistically at the whole ecosystem. In fact, NREL is leading BOTTLE, a consortium of national labs, universities, and others working on innovative upcycling technologies for today's plastics and redesigning tomorrow's plastics to be recyclable by design. Our work in BOTTLE tremendously amplifies what we can accomplish through collaboration with our talented, multidisciplinary research partners in the consortium.
Combine that with partnerships with some industrial players who understand in great detail certain elements of technology, and really fantastic things can happen. We have the tools here to mount serious efforts at solving some of these grand challenges associated with plastic waste and the circular economy.
What difference will this research make in the lives of individuals and the future of our planet that might not be as obvious?
One thing we're incredibly interested in right now is microplastics, those tiny plastic particles that come from discarded waste. A bottle floating in the water is unsightly, but it can become even more concerning if that bottle degrades into microplastic.
Those miniscule fragments can get into the food supply for wildlife and for humans. Our team thinks we can eliminate a significant percentage of microplastic by keeping the material from entering the waste stream.
What do you see as the key to true innovation?
Innovation can come out of an attempt to do something really heroic, such as trying to come up with a completely new process to recycle plastic bottles. But you have to work with other dedicated people who have a lot of expertise in that particular technology to uncover and overcome potential impediments. When you hit problems, that's where innovation takes place.
What we're trying to do is big, big, BIG. Its success will rely on more than just a small handful of chemists or biologists.
You need to form partnerships with experts in that area early on, and you also need a diversity of voices and experiences. Then, your ideas will really evolve, and innovation will occur.
Learn more about NREL's involvement in the Bio-Optimized Technologies to keep Thermoplastics out of Landfills and the Environment (BOTTLE) Consortium, plastics upcycling innovations, and projects focused on the circular economy.
Last Updated May 28, 2025