Why the World Needs Manufacturing Masterminds
Six Masterminds Share How They Are Cleaning Up Greenhouse Gases, Plastics, and Waste—And How They Built Their Planet-Saving Careers
How do we prevent blackouts? Clean up smog in our air and plastics in our waterways? Or build clean energy technologies while reducing waste? In other words, how do we change the world?
Hint: Hire a mastermind—a manufacturing mastermind.
Launched in late 2021, a new profile series called Manufacturing Masterminds is showcasing what the National Renewable Energy Laboratory’s (NREL's) advanced manufacturing chemists, analysts, engineers, and leaders are up to. Our masterminds also share how they built their careers, what advice they have for future masterminds, and which podcasts they listen to on the way to work (spoiler alert: a certain New York Times daily is a popular choice).
So far, six masterminds have shared how they are reducing waste and emissions in the manufacturing industry (while making sure Americans get the goods they need), creating plant-based plastics (or reinventing those that are polluting in the world), and building recyclable renewable energy technologies (to help the grid go carbon-free). Sprinkled into their master plans are child-sized zucchinis, toy plants, ice axes, plastic-eating microbes, rickety (yet inspirational) power grids, television shows, a landfill epiphany, and a wee island with no stoplights.
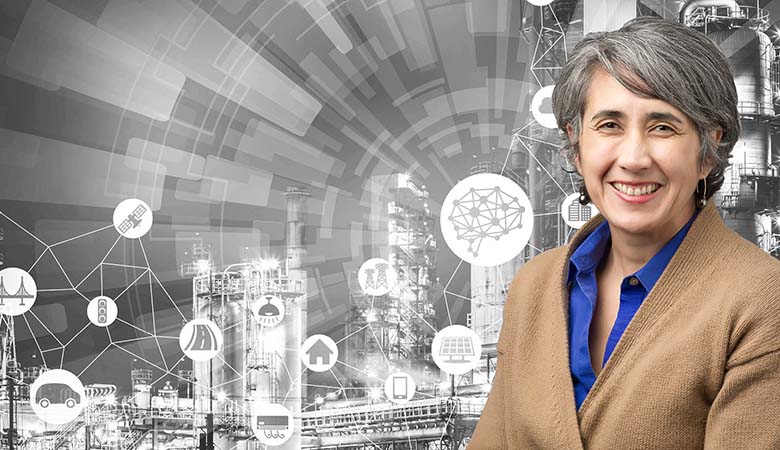
That island is where Alberta (Birdie) Carpenter, a senior environmental engineer at NREL and the series’ first subject, grew up. As a child, she bounced from place to place and yet always considered the small island of Saipan, which had yet to install stoplights during her youth, to be her true home. Carpenter’s web-like nomadic childhood is a kind of carbon copy of what she studies today: the tangled, global carbon footprints the manufacturing industry leaves in its tracks.
“Manufacturing uses a lot of really nasty stuff and produces a lot of pollution,” Carpenter said in her Manufacturing Masterminds profile. “So, how do we do better? How can manufacturing be part of ecosystem services so they're not degrading the ecosystem but rather bolstering it or improving it?” she said. “There’s no one-size-fits-all solution.”
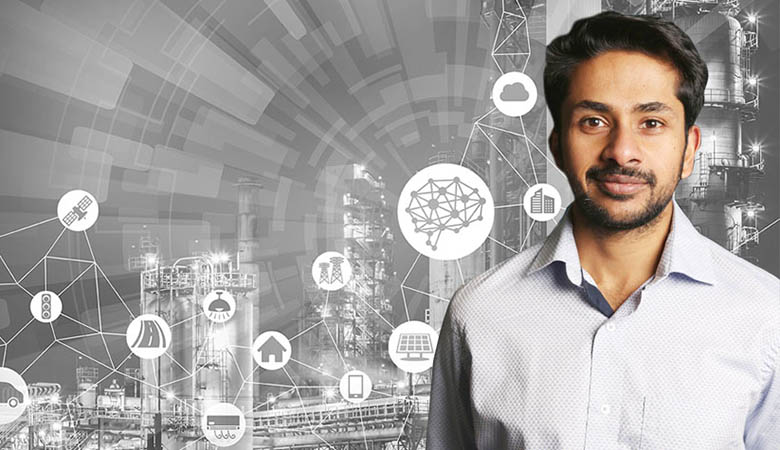
Each jug of milk, leather (or faux leather) jacket, and gas or electric car carries a carbon footprint, which starts at the mine and ends in the landfill or recycling center (if recycling is an option). Even solar panels and wind turbines have their own complex footprints. Each footprint comes with a cost, too, which is where mastermind Parthiv Kurup, a cost and systems analyst at NREL, comes in. “For somebody to buy it, it has to make sense,” Kurup said in his Q&A profile.
Growing up in India in the 1980s, a young Kurup witnessed planned blackouts—meant to protect a shaky power grid—but also unplanned blackouts, which happened when those protections failed. These dark spells inspired him to join the energy industry and, eventually, renewable energy, which he believed made more environmental and economic sense. Today, he analyzes the energy and financial costs behind renewable energy technologies to make sure consumers, industries, and countries understand their value.
“As Wayne Gretzky put it: ‘Skate where the puck is going, not where the puck has been,’” Kurup said. “Renewable energy is where the puck is going.”
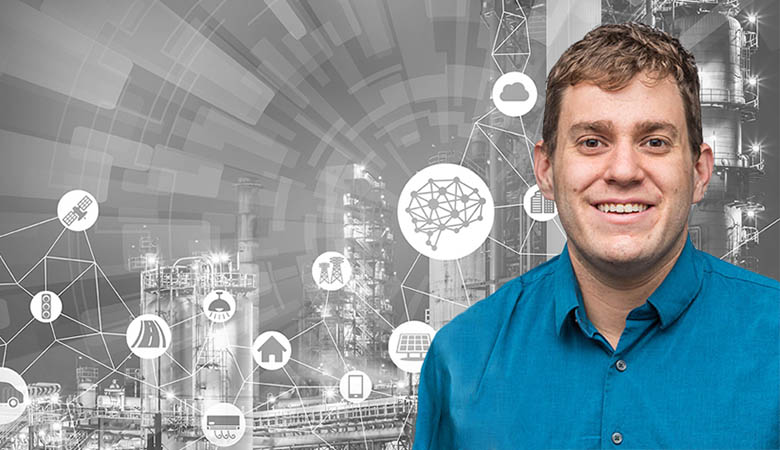
Plastics could be, too, if Nic Rorrer's predictions are right. “It’s very possible our future society runs on plastics,” Rorrer, a senior researcher at NREL, said in his interview. “I’m not going to lie and say we do a good job of handling end-of-life materials. It’s terrible. But that’s true for a lot of things, like my metal water bottle, food waste, and sustainable fuels and products. So, the question is: How do I redesign plastics to be reused?”
Rorrer is working to answer that question, exploring new plant-based plastics built from corn and sugar as well as identifying new methods to break down and reuse today’s most plentiful (and toughest) plastics with, for example, plastic-munching microbes. His dream is to one day strap on a snowboard made from his very own plant-based resins.
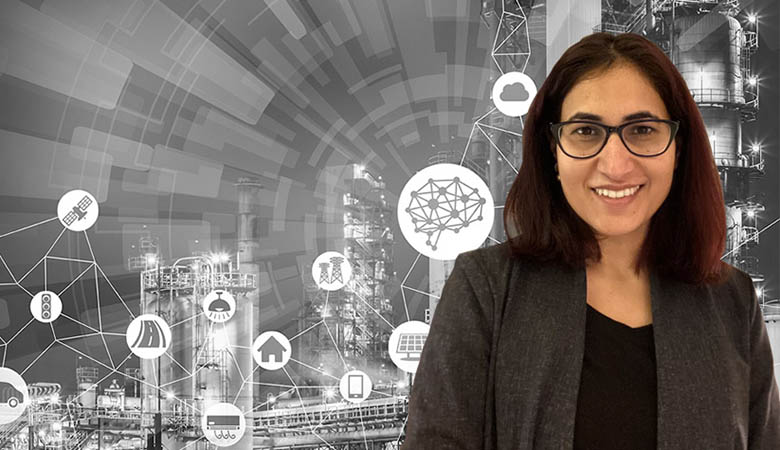
Chemical engineer Avantika Singh could help Rorrer realize that dream—because she’s well on her way to achieving hers. Early in her career, Singh took a tour of landfills, composting facilities, and other waste-processing plants in her native country of India to learn where garbage goes. After climbing mountains of reeking trash full of recyclable plastics, she made a promise to herself: “If I can change any part of that, any tiny part of that, that’s what I’ll do.”
Now a member of the Bio-Optimized Technologies to keep Thermoplastics out of Landfills and the Environment (BOTTLE™) consortium, Singh works with Rorrer to design new ways to transform, recycle, and reuse plastics—like the common carbon-based plastics found in clothes, carpets, and bottles—before they end up in mountainous landfills. “I hate waste. I absolutely hate waste,” Singh said to explain both her career and life decisions. “If there's anything I can do to prevent it, recycle it, or upcycle it, I want to do it.”
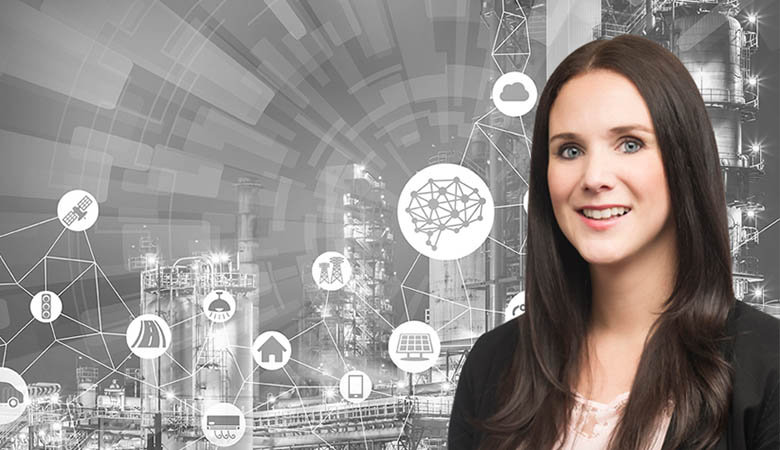
Another waste-reduction champion, Robynne Murray, is already manufacturing award-winning materials. Her team’s new thermoplastic resin could be used to build recyclable and potentially more cost-effective and durable wind turbine and tidal turbine blades. A “bit of a rebel” in high school, Murray thought she’d never end up at NREL. “If I knew I would be doing something useful and meaningful in my life, I would have had a lot more confidence back then,” Murray said about her path to renewable energy research.
Now, Murray gets her hands dirty inside and outside the lab, manufacturing and evaluating new materials (like a new plant-based resin) or climbing rock and ice crags, skiing through the Alps, and clam digging in Canada’s Bay of Fundy where she grew up—a place she hopes will one day host tidal turbines she helped build.
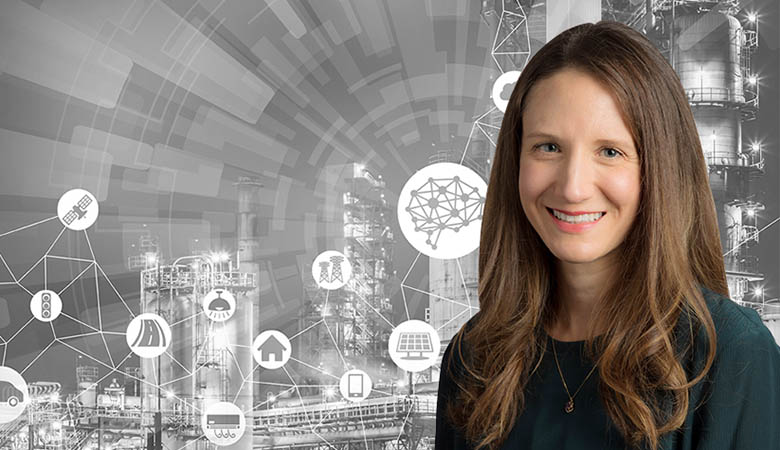
When NREL materials chemist Meredith Doyle was a kid, she also got her hands dirty. The budding scientist conducted experiments to see how big she could grow a zucchini (check out the child-sized gourd in Doyle's Q&A profile). Now, as the project manager and chief operating officer of the BOTTLE consortium, Doyle leads an interdisciplinary team of more than 100 researchers from national laboratories, academia, and industry. Together, they are inventing solutions to break down or recycle plastics and reduce the energy needed to manufacture them, too.
“I wanted to work on something big, something that will help the world, and help people,” Doyle said. She, like Singh, got her wish. Doyle helps search for solutions to plastics waste, one of the biggest, most urgent global challenges, one that has infiltrated not just landfills but also oceans, rain water, and fish worldwide.
“Plastics have revolutionized our society,” Doyle said. They transformed food storage and medical treatments. But plastics waste—especially from single-use plastics—is piling up around the world. Still, Doyle is optimistic: “I really do think we’re going to help change the world.”
Learn more about NREL’s Manufacturing Masterminds Q&A profile series.
Last Updated May 28, 2025