NREL Selected To Design Next-Generation Power Inverters for US Combat Vehicles
New Silicon Carbide-Based Propulsion System Will Deliver Four Times the Power at a Fourth of Predecessors’ Size
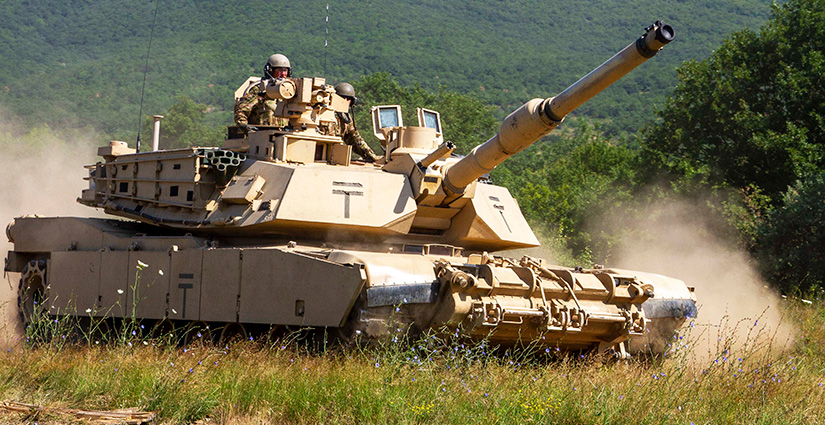
A new silicon carbide (SiC)-based inverter design from NREL’s power electronics researchers will give U.S. military ground combat vehicles 200% greater range at a fourth of the size of predecessor technology. Image by Army Staff Sgt. True Thao
To design the vehicles of the future, you might think you need a sweeping overhaul of the entire system. But sometimes, reimagining a single component can lead to transformational results.
To transform United States military ground combat vehicles, the National Renewable Energy Laboratory (NREL) has been selected to redesign a critical component: the traction inverter, which controls the flow of electricity between a vehicle’s battery, motor, and drivetrain. The new silicon carbide (SiC)-based propulsion system will double the range of Army vehicles with a footprint four times smaller than its predecessors.
The three-year, $6 million project has been fully funded by the Operational Energy Capability Improvement Fund (OECIF), which guides energy innovations for the United States Department of Defense. It will be led by the United States Army Combat Capabilities Development Command, known as DEVCOM, with researchers from both NREL and the Army Research Laboratory (ARL) providing technical expertise.
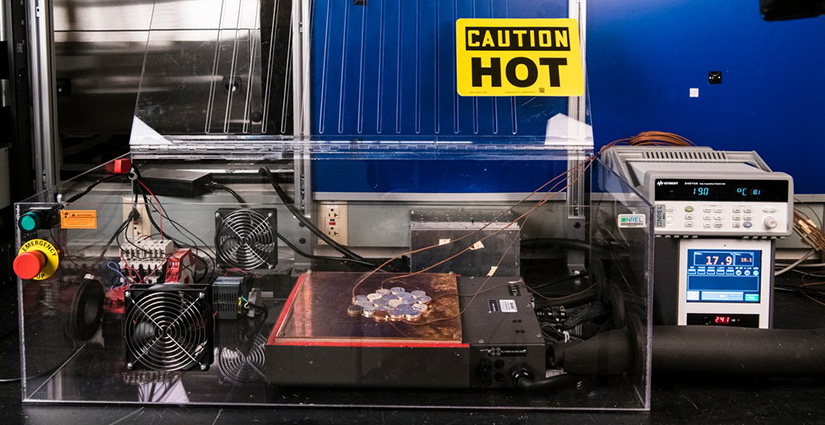
NREL researchers will apply their expertise in power electronics thermal management research to thoroughly validate PICHOT's innovative cooling system. Image by Dennis Schroeder, NREL
The inverter will be designed, fabricated, and characterized in house at NREL prior to evaluation at the U.S. Army Ground Vehicle Systems Center's test labs. Its modular design will allow it to slot into many different hybrid-electric ground combat vehicles, from light- to medium-wheeled vehicles to Abrams and Stryker battle tanks. SiC-based semiconductors and novel thermal management will give it unmatched power density, allowing vehicles to travel farther with less fuel.
“Any one of the innovations we’re incorporating into PICHOT would be an accomplishment,” said Brian Miller, a power systems engineer within NREL’s Energy Security and Resilience Center who will help guide the PICHOT project. “We’re adding six.”
Put simply, PICHOT represents a new frontier for power electronics—and for ground combat vehicles.
Reimagining Propulsion System Power Electronics
To create PICHOT, NREL’s power electronics are reimagining nearly every aspect of conventional power inverters.
First, researchers studied the current leading traction inverter used by U.S. Army ground combat vehicles: the 200-kilowatt Zeus inverter, created by DEVCOM for high-power applications. Then, based on NREL’s world-leading research into power electronics thermal management, they determined everything they could strip away from the predecessor technology—from the cooling equipment to the connectors.
Because traction inverters are typically installed next to other heat-generating elements in a combat vehicle, they need to be able to withstand high operating as well as ambient temperatures. This usually requires them to be packed with bulky cooling technologies, like cold plates or coolant reservoirs.
PICHOT will require none of these heavy cooling solutions. Instead, it will link to the existing engine coolant system, eliminating the need for additional coolant loops. In turn, unlike conventional silicon-based inverter systems—which become essentially powerless when exposed to operating environments over 70°C—PICHOT will be able to function at full power in environments of 105°C.
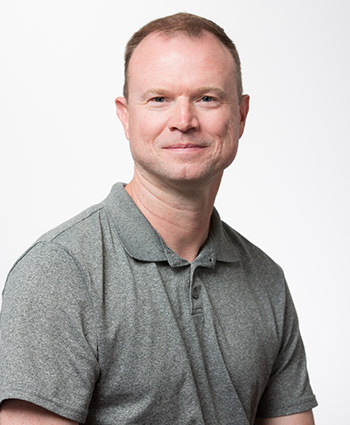
NREL’s Brian Miller will help lead the laboratory’s contributions to the project. Image by Gregory Cooper, NREL
Most importantly, PICHOT will enable 53% fuel savings compared to existing technologies, meaning Army vehicles will be able to stay in the field for nearly twice as long before needing to refuel. Combined with silent performance thanks to the hybrid-electric engine and electromagnetic interference shielding, Army ground combat vehicles are poised to become safer, longer-range, and higher-performing than ever before.
“NREL is home to a highly skilled thermal management research group,” said Faisal Khan, chief researcher of power electronics within NREL’s Center for Integrated Mobility Sciences, who will serve as principal investigator for the project. “Given the complexity of this project—designing a high-power-density traction inverter with stringent thermal management that can function in extreme environments—we are well equipped to handle this challenging work.”
Powering Forward

NREL’s Faisal Khan will lead the laboratory’s contributions to the project and serve as the primary investigator. Image by Agata Bogucka, NREL
PICHOT will take three years to design, fabricate, and evaluate. In the first year, NREL researchers will build a computer-generated model of the inverter and simulate its operations in the real world, ensuring that it will operate as planned. Then, they will build it using the laboratory’s end-to-end prototype fabrication pipeline and demonstrate its effectiveness versus other combatants’ standard vehicles.
Finally, the blueprints will become available to manufacturers at a forthcoming industry day. The final design will be manufactured at scale, with potential to be leveraged in multiple kinds of U.S. Army ground combat vehicles.
And as the Army prepares to implement climate strategies aligned with the nation’s shift to lower-emitting vehicles, it will find that new solutions, powered by clean energy, will provide more power, reliability, and sustainability than ever before.
Learn more about NREL's sustainable transportation and mobility research and its specific focus on advanced power electronics and electric machines. And sign up for NREL's quarterly transportation and mobility research newsletter, Sustainable Mobility Matters, to stay current on the latest news.