Q&A With Ana Aday: A Holistic Approach To Advancing Cement and Concrete Sustainability
Aday Leads Research and Development of Cement and Concrete Alternatives To Decarbonize the Value Chain of Industrial Processes
When people think of the National Renewable Energy Laboratory (NREL), it is often solar, wind, and other clean energy generation technologies that come to mind. However, Ana Aday, a materials science researcher in NREL’s Building Technologies and Science Center, is taking on a whole new challenge: decarbonizing the cement and concrete industry.
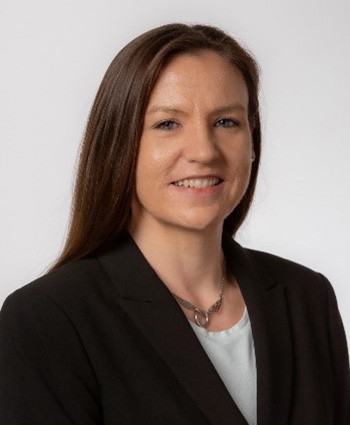
In late March, Aday presented the work that she and fellow NRELians have been tackling during the American Concrete Institute’s Convention, one of the biggest cement and concrete conferences for academia and research in the country. The following is an interview with Aday.
How would you describe your research in low-carbon cement and concrete?
At NREL, we take a holistic approach to decarbonizing cement and concrete production by considering and addressing the entire value chain, the circularity of industrial processes, and how they are interconnected. Greenhouse gas (GHG) emissions are prevalent in all stages of production and not just one aspect of the ecosystem. The traditional cement production process is a global contributor of GHGs, accounting for roughly 8% of global GHG emissions.
The breakdown of GHGs in cement production is roughly distributed between the extraction of raw materials at about 3%, about 85% from the production of clinker and the heating of the calciner, and about 12% from the downstream process (including cooling and transportation logistics). Of the 85% of GHG emissions from the direct production of cement, about 34% of CO2 emissions are from the use of fossil fuels to heat the kilns and the remaining 51% come from the calcination of the raw feedstock materials. But even with the best energy efficiency technologies, we need to target the materials process that represents 50% of CO2 emissions to provide decarbonization solutions to the entire carbon dioxide challenge.
So as a materials scientist, it is my job to analyze the unique structure, process, properties, and performance of mixing concrete and cement alternatives. We also are considering carbon capture, utilization, and storage techniques to mineralize CO2 emitted into supplementary cementitious materials (SCMs), additive manufacturing techniques (e.g., 3D printing), how we can reduce the waste and leftover materials from processing, and the environmental impacts that are associated with raw material extraction.
Can you elaborate on NREL’s unique and critical role in the development and deployment of low-carbon cement and concrete alternatives?
NREL and national labs have a unique opportunity to face the cement and concrete decarbonization challenges with a long-term vision by spending time on innovations that have a low to mid technology readiness level. We understand the need for private industry to maintain a return on their investments, which requires them to integrate technologies that are market ready with limited to no risk.
We sit at the “in-between” where we can bridge the gap between basic science and novel technologies that often fall in the “valley of death” and de-risk technologies making them more appealing for commercialization. We approach our research with objectivity and are not required to be competitive with our work, so we look at all potential solutions and bring all private and public organizations’ priorities to the table. Essentially, we wear a research and business hat simultaneously. So, wherever an organization lives in the value chain, they can partner with NREL.
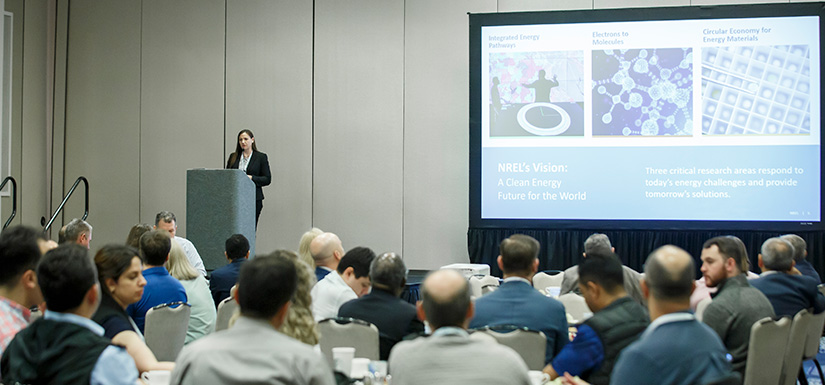
What do you view as the largest challenge for low-carbon cement and concrete alternatives?
The largest challenge is the deployment of lab-tested technologies into the real world. There are several steps that need to take place for companies to begin specifying and using cement and concrete alternatives including procurement, the production of materials, and the approval process from third-party verification (e.g., ASTM International).
At NREL, we can develop and have experimental control over many variables in the concrete, such as optimal mixing and curing conditions, whereas the contractors placing concrete in the field are subject to the environmental elements that day. For concrete production facilities, their infrastructure may not be as up to date and they may also have challenges obtaining alternative feedstocks, thereby making it difficult to replicate laboratory results in real-world construction. And just because we can produce it in the lab does not mean it will be a one-for-one replacement at the construction site. This is because many factors affect the placement of concrete outdoors including weather (i.e., wind, humidity, surface temperature, and air temperature).
Regarding the approval process, there are structural standards that must be met, requiring material submission to third-party testing labs, which may take a few years to receive the thumbs up. This is where NREL steps in. By evaluating the entire value chain, we can identify those challenges and develop solutions to make real-world deployment opportunities feasible.
What do you wish people understood about cement and concrete and efforts to decarbonize this industry?
The largest hurdle for this industry is identifying and understanding the complexities of the value chain and how they are interconnected. We are taking this head on by hosting listening sessions and customer discovery interviews with public and private organizations, which provides stakeholders an opportunity to voice their individual concerns. For example, an organization at our most recent listening session explained that they only have the infrastructure to house two types of SCM at their production facility and had no additional space for new SCMs. So, learning about these constraints helped us understand procurement challenges for smaller companies.
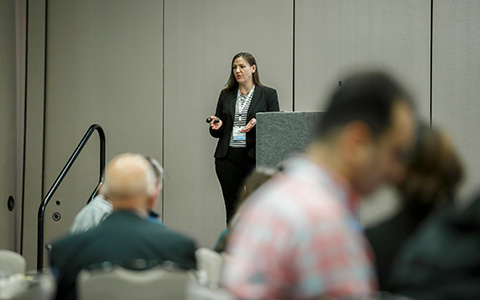
What were your goals when speaking and networking at the American Concrete Institute convention?
Our end goal for presenting at the ACI convention and connecting with organizations was to introduce NREL to the cement and concrete community. It is imperative that our potential partners understand the capabilities we have at the lab to test and demonstrate these technologies. We want to accelerate the discussion around novel and alternative clean energy practices in this industry.
What were the takeaways you wanted audience members and potential partners to consider from your keynote speech?
The main takeaway is that NREL is addressing a large range of decarbonization solutions across the supply chain. We do not want anyone to feel left behind. This industry has supplied a large number of American jobs for decades, and our community members must continue being employed. So, considering elements like workforce training while we continue researching and developing cement and concrete alternatives is always at the top of our minds.
What does partnering with NREL look like?
From a partner perspective, we handle a lot of logistics and project management, along with development and de-risking the deployment of the technology. The reason we partner with industry is so they can feel confident that they can successfully deploy the technology and minimize hiccups. With this type of work, the partner can engage in a hands-on fashion, and I have great commercial partners that contribute to materials testing or manufacturing. A great sign has been when I reach out to potential partners, current and new, I am often met with enthusiasm and willingness to partner. A specific example is a company that I partnered with on a Funding Opportunity Announcement (FOA) is now reaching out to me to partner on other FOAs.
We also encourage potential partners to visit our campus in Golden, Colorado. We enjoy hosting organizations and individuals so that they can visualize and learn about the breadth of work taking place at our lab that spans from analysis and modeling to in-the-field testing of novel technologies.
What do you find most promising in the concrete and cement space?
What has been the most promising is our industry shifting their mindset about integrating new materials and processes to decarbonize the production of cement and concrete. In previous decades, this was a difficult conversation to broach, but clean energy integration is far more accepted by private and public industry. There is a large volume of startups and different technologies that are addressing all aspects of the value chain and could be used to decarbonize this industry. The momentum we are seeing is promising for industrial transitions and transformation.
Learn more about Ana's work and how you can collaborate with our experts.
This article has been updated to reflect an editorial change made after its original publication.