With a Technology License From MIT and NREL in Hand, Comstock Fuels Aims To Produce Jet Fuel From Lignin
Patent-Pending Technology Turns Lignin—a Plant Structural Material—Into Aromatic Hydrocarbons That Could Help Leap Over Synthetic Aviation Fuel ‘Blend Wall’
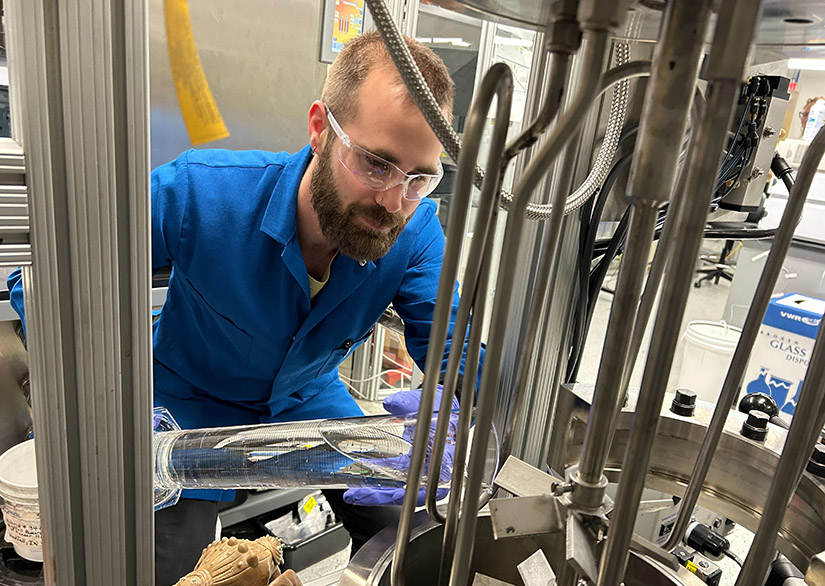
NREL research technician Spencer Lask prepares feedstock for hydrodeoxygenation using a batch pressure reactor—allowing NREL to work in parallel with industry partner Comstock Fuels. Photo by Mickey Stone, NREL
It is an ideal complement to Comstock Fuels’ own technologies: an additional refining step to upgrade lignin from biomass into aromatic hydrocarbons, which are molecules needed to produce “drop-in” synthetic aviation fuel (SAF).
SAF can be made with abundant biomass and waste resources from America’s farms, forests, and waste facilities. However, most SAF today must be combined with petroleum jet fuel (Jet A) to meet strict performance requirements for aviation. This is because jet engines need fuel that contains a blend of hydrocarbons for safe operation—alkanes (including n-alkanes, isoalkanes, and cycloalkanes) and aromatics. To date, most SAF production processes yield fuels rich in n-alkanes and isoalkanes, but pathways for producing aromatics and cycloalkanes are scarce.
But the SAF technology being codeveloped by the Massachusetts Institute of Technology (MIT) and the National Renewable Energy Laboratory (NREL) is different. It yields aromatic-rich SAF by deconstructing lignin in plants and hydrodeoxygenating the resulting molecules to jet-range blendstocks.
Understanding that SAF needs to comprise roughly 20% aromatics, Comstock Fuels President David Winsness jumped on the opportunity to scale up the technology. In September 2024, Comstock Fuels signed a cooperative research and development agreement with MIT and NREL.
If the MIT–NREL technology is successfully scaled up and integrated into Comstock’s existing processes, the combination of technologies could help address the so-called SAF “blend wall”—providing a path toward SAF that is functionally identical to Jet A.
A Chance Encounter Sparks Research Agreement
Winsness discovered the patent-pending MIT–NREL lignin conversion technology during an exploratory meeting at NREL’s Golden, Colorado, campus, where he was discussing scaling up Comstock’s Bioleum SAF technology. During that meeting, NREL Principal Scientist Robert Baldwin introduced Winsness and his colleagues to the new lignin pathway and recommended an introduction to NREL Senior Research Fellow Gregg Beckham and NREL chemical engineer and group manager David Brandner, who together lead NREL’s component of the work with a team of researchers.
A veteran of the biofuels industry, Winsness had himself developed and commercialized a patented process that recovers distillers corn oil from corn ethanol facilities for use in producing additional fuels, increasing yields and revenues. Upward of 95% of the U.S. corn ethanol industry uses the technology today. Winsness and his team then set their sights on lignin as their next innovation on the belief that doing so could support petroleum, pulp and paper, forestry, and other relevant industries.
After more than 10 years, they developed a patented and patent-pending process that extracts and converts lignin into an intermediate called Bioleum. In an August 2024 press release, the company reported yields of cellulosic ethanol and Bioleum-derived fuels exceeding 125 gallons per metric ton of biomass (on a gasoline-gallon-equivalent basis), depending on feedstock, lignin content, site conditions, and other process parameters.
After Baldwin’s initial introduction to Beckham and a series of follow-up communications, it became clear that the MIT–NREL lignin-based SAF technology could complement Comstock’s processes by refining Bioleum further to produce both alkane and aromatic SAF. The parties recently executed an exclusive license agreement, in addition to the research agreement, just six months after their first meeting.
At its pilot facility in Wisconsin, Comstock Fuels is currently scaling up and demonstrating its Bioleum technology to convert woody biomass into SAF. One step of Comstock’s chemical processes isolates lignin by separating it from the other major plant polymers—the polysaccharides cellulose and hemicellulose—which continue through the process for conversion into alkane SAF.
“The type of digestion we are already doing is ideal for MIT and NREL’s technology,” Winsness said.
It was there—where Comstock produces a stream of lignin—that Baldwin and Winsness saw an exciting interdependency and linkage point.
“MIT and NREL’s technology makes a highly aromatic blendstock, but that's great because most of the other SAF technologies out there today make blendstocks that don't contain aromatics,” Baldwin said. “To get 100% SAF, you have to have some source of aromatics, and one way to get them is from lignin.”
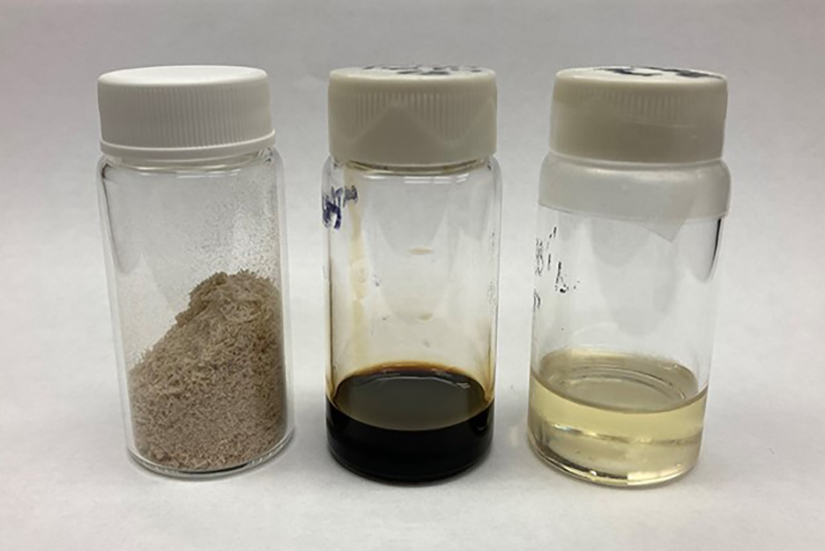
From Lignin to Highly Aromatic SAF
Lignin—which makes up around 30% of biomass—is a complex polymer that supports plants and helps them resist decay. Based on projections of future feedstock supply, which are outlined in the U.S. Department of Energy’s 2023 Billion-Ton Report, lignin could generate as much as 63 billion gallons of SAF annually by 2040—three times more fuel than U.S. airlines consumed in 2019.
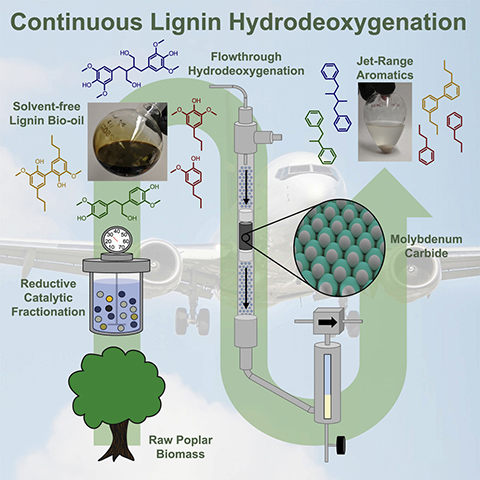
However, for years the industry has lacked the key for unlocking that potential. Researchers continue to search for economical methods for turning lignin into useful products, including the aromatic hydrocarbons needed for SAF. In the pulp and paper industry today, lignin is burned for heat, though NREL and other researchers are also developing technologies for turning waste lignin into valuable bioproducts.
However, building on advances in catalysis, a multi-institution team of researchers, including MIT’s Mickey Stone, Matt Webber, and Yuriy Román-Leshkov, unveiled a study with the potential to overturn that dynamic. With support from the U.S. Department of Energy’s Bioenergy Technologies Office, they demonstrated a method for removing oxygen from lignin and a catalyst to refashion the resulting molecules into an aromatic-rich SAF blendstock—an additive for mixing with alkane SAF.
First described in a 2022 Joule article, the technology combines alcohol extraction of lignin from biomass with an Earth-abundant hydrodeoxygenation catalyst to stabilize the extracted lignin and produce an oil enriched with aromatics. Importantly, this catalyst resists deactivation or poisoning from impurities often present in biomass.
Having successfully demonstrated the technology in the lab, MIT and NREL filed a patent application for the technology. Now, to show its value outside the lab for the biofuels industry, it is time to scale it up.
The Three-Year Plan: Scaling It Up
Over the next three years, Comstock will build a pilot-scale version of the MIT–NREL lignin conversion technology, a task that involves linking the various steps into an uninterrupted process that can run continuously. They will also incorporate larger reactors and equipment, moving from producing milliliters of the aromatic SAF blendstock to a few gallons.
That process will provide Comstock with valuable data and engineering designs to consider as it works to integrate it with its own Bioleum technology. Winsness said that the MIT–NREL process can be added with a few minor modifications to accept the existing lignin stream.

“We already have over 2,000 runs on our pilot reactor and a tremendous amount of data,” Winsness said. “We think we can take the MIT–NREL process from a technology readiness level (TRL) of 4 to 6 very quickly if all goes well.”
Of course, that would not be the end of the systematic process for demonstrating and commercializing the technology. After successfully piloting the MIT–NREL process at TRL 6 and 7, Comstock would then need to integrate the process into even larger facilities in the coming years, elevating the Comstock and MIT–NREL processes to TRL 8 and 9. Comstock Fuels plans to license the technologies globally and to build, own, and operate its own network of Bioleum refineries in the United States with several sites under evaluation for construction of its initial demonstration-scale facility—paving the way for commercialization.
Success could put millions of more gallons of SAF into the marketplace, according to NREL senior licensing executive Eric Payne.
“It’s not every day the lab gets a partner like Comstock who’s ready to jump in and fund technology scale-up, which is so critical for commercialization,” he said. “They’ve got the potential to impact billions of gallons of SAF, and that is really exciting. This is a huge market.”
Learn more about NREL’s biofuels and bio-based chemicals research, as well as the laboratory’s broader advanced aviation research.