Distributed Wind Aeroelastic Modeling
Through the Distributed Wind Aeroelastic Modeling (dWAM) project, NREL researchers are helping provide the distributed wind energy industry with better tools to model, validate, and certify improved wind turbine designs.
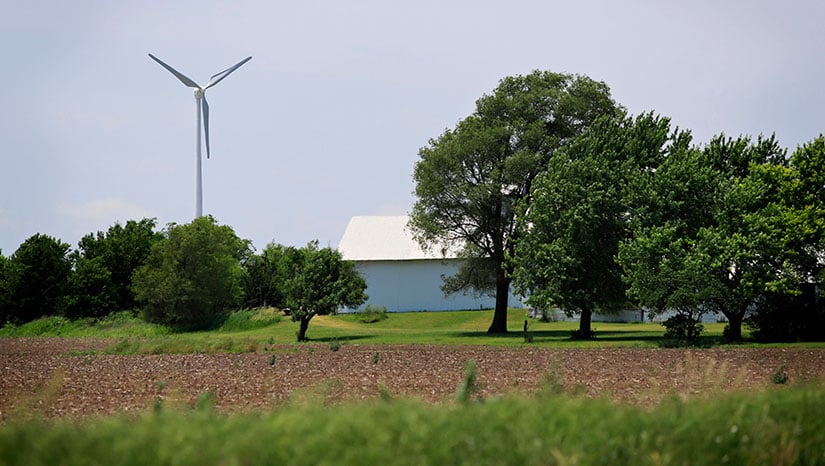
The Distributed Wind Aeroelastic Modeling project helps improve the tools used to design small-scale wind turbines for distributed energy systems at farms, communities, or homes, like this one in Kansas. Photo from Eocycle Technologies
Distributed Wind Aeroelastic Modeling Webinar
NREL and Sandia National Laboratories researchers held a webinar Sept. 26, 2024, to share new distributed wind aeroelastic tools with the modeling community.
Unable to attend the live event? Watch the webinar recording.
To ensure distributed wind turbines are resilient, stable, and high performing, new designs undergo an evaluation to check loads on the turbine components and results of field testing. Before building a costly prototype for testing, turbine designers can use aeroelastic modeling to see how a turbine will function when subjected to winds over its lifetime. Aeroelastic models simulate airflow and turbine behavior for land-based and offshore wind turbine designs. These models have been modified for small- and medium-sized wind turbines used in distributed wind energy applications, providing on-site power for farms, houses, and communities.
Through the dWAM project, which is funded by the U.S. Department of Energy's Wind Energy Technologies Office, NREL researchers, along with collaborators at Sandia National Laboratories and several industry companies, are working to improve aeroelastic modeling for distributed wind turbines. Their goal is to provide the tools turbine suppliers need to design and certify optimized and reliable small- and medium-sized wind turbines with competitive costs of energy.
Project Approach
During this 3-year project, researchers are working to improve the physics of models for several types of distributed wind turbine designs (called archetypes), including both horizontal- and vertical-axis wind turbines, many of which are part of the NREL Competitiveness Improvement Project.
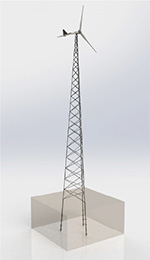
A: Bergey Excel 15
Passive-yaw, upwind, stall-regulated, horizontal-axis wind turbine. Photo from Bergey WIndpower Co.
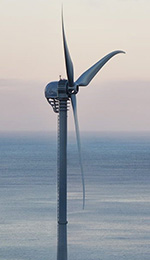
B: Eocycle EOX M-26
Passive yaw, downwind, stall-regulated, horizontal-axis wind turbine. Photo from Eocycle Technologies
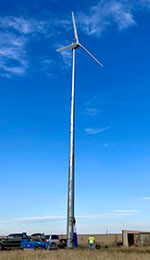
C: QED PHX-20
Active-yaw, upwind, stall-regulated, horizontal-axis wind turbine. Photo from QED Wind Power
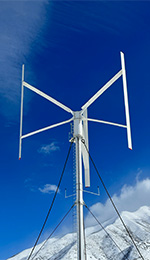
D: XFlow Energy
XFlow installed a prototype 25-kW vertical-axis wind turbine at Windward Engineering's test facility in Spanish Fork, Utah, for vertical-axis wind turbine model validation. Photo from XFlow Energy
Three modern distributed wind turbines (A, B, and C) installed at NREL's Flatirons Campus under the Flatirons Distributed Wind Turbine Installation project serve as the baseline for new reference turbines and for model validation.
Researchers have created validated advanced reference turbines for popular distributed wind turbine designs. This GitHub repository contains aeroelastic models of distributed wind reference turbines and other publicly available aeroelastic models for distributed wind archetypes.
Once validated, the team will update the tools for improved user experience (such as by revising documentation for NREL's OpenFAST).
Through this project, researchers are enabling industry adoption of the upgraded modeling tools to develop certified wind turbines that perform better, are more reliable, and generate energy at a lower cost, with the goal of accelerating distributed wind energy deployment across the United States.
Project Components
To reach the project's goals, researchers are:
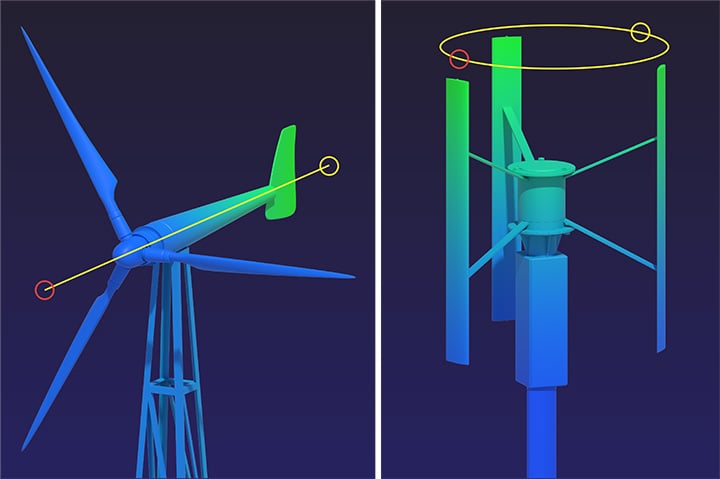
NREL and Sandia National Laboratories researchers are working with industry partners to improve modeling tools to validate better-performing, more reliable, and lower-cost distributed wind turbines. Images by Besiki Kazaishvili, NREL
- Focusing on modern, horizontal-axis archetypes
- Improving OpenFAST code
- Validating code improvements using research turbines at NREL's Flatirons Campus
- Verifying that the results from different modeling tools agree
- Developing guidance documents and upgrading user manuals.
To address vertical-axis wind turbine modeling, the team is also:
- Improving modeling code and user experience in collaboration with Sandia National Laboratories
- Coupling Sandia National Laboratories' Offshore Wind Energy Simulator code and NREL's OpenFAST and AeroDyn software tools.
To improve automated Campbell diagram capabilities, the team is also:
- Developing a streamlined, documented, and automated procedure to generate a Campbell diagram (which charts the turbine's response to vibration stress at various levels of operation)
- Helping turbines meeting the certification requirements in International Electrotechnical Commission standards.
And finally, the team is launching the improved tools by developing guidance on distributed wind turbine modeling.
Publications
Design Load Basis Guidance for Distributed Wind Turbines, NREL Technical Report (2024)
NREL 15-kW: An Advanced Horizontal-Axis Reference Turbine for Distributed Wind, Journal of Physics: Conference Series (2024)
Critical Design Load Case Fatigue and Ultimate Failure Simulation For a 10-m H-Type Vertical-Axis Wind Turbine, Journal of Physics: Conference Series (2024)
Modeling the Yaw Behavior of Tail Fins for Small Wind Turbines: November 22, 2021–May 21, 2024, NREL Technical Report (2023)
Distributed Wind Aeroelastic Modeling Fact Sheet, NREL Fact Sheet (2023)
Distributed Wind Aeroelastic Modeling Presentation, Distributed Wind National Laboratory–Industry Discussion (2023)
Aeroelastic Modeling for Distributed Wind Turbines, NREL Technical Report (2022)
Partners
Partners on this project include:
- Sandia National Laboratories
- Technical University of Denmark
- RRD Engineering
- Windward Engineering
- Advanced Renewable Technology
- Bergey Windpower Co.
- QED Wind Power
- Eocycle Americas
- XFlow Energy Co.
- University of Calgary
- University of Massachusetts Amherst.
Contact
Share
Last Updated Feb. 19, 2025