Dynamometer Research Facilities
NREL's dynamometer research facilities validate power-train and power-take-off systems with controlled, full-scale, real-world loading scenarios.
NREL's Flatirons Campus performs research validation on wind turbine drivetrains from 1 kW to 5 MW for the U.S. Department of Energy and our industry partners. Our dynamometer research facilities can assess a variety of components and subsystems, including generators, gearboxes, power converters, bearings, brakes, lubrication, cooling, and control systems. Manufacturers and design engineers use our facilities to perform accelerated lifetime experiments, develop customized software, and study generator and power electronics system performance and grid integration.
Mechanical and Electrical Power System Validation
NREL's dynamometer research helps ensure wind turbine reliability, which reduces both risk and cost. In a typical dynamometer assessment, a powerful motor replaces the rotor and blades of a wind turbine. This simulation of real-world conditions allows researchers to:
- Validate innovative prototypes against models and design assumptions
- Optimize electro-mechanical and control systems for reduced levelized costs of energy
- De-risk full-scale systems in a controlled, easily accessed environment prior to deployment on tower or at sea.
Infrastructure and Hardware
NREL is one of only a handful of facilities in the world with the dual capability of simulating the rotation and bending that a wind turbine rotor places on a drivetrain. Our three dynamometer research facilities include:
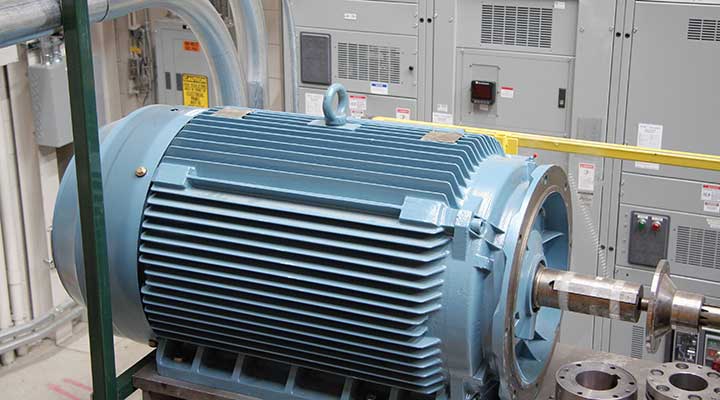
225-kW Dynamometer
Ideal for smaller turbines, this dynamometer employs a 300-horsepower (hp) variable-speed induction motor with a variable-frequency drive and alternating-current (AC) grid connections of 120 volts (V), 240 V, and 480 V.
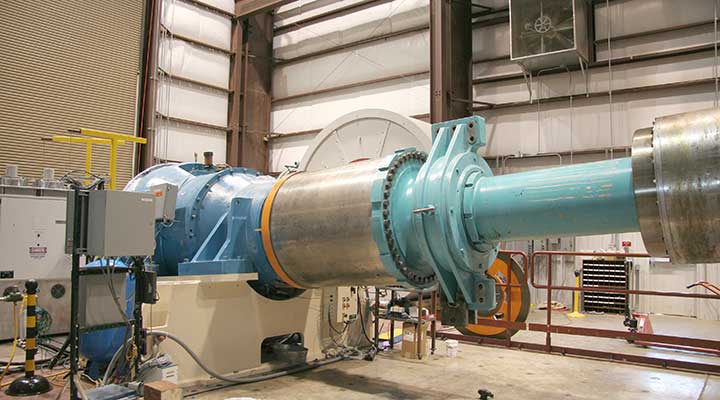
2.5-MW Dynamometer
A practical size for most of today's land-based wind turbines, the 2.5-MW dynamometer features a 3,351-hp, AC induction motor with a variable-frequency drive, and 480 V, 690 V, and 13,200 V AC grid connections.
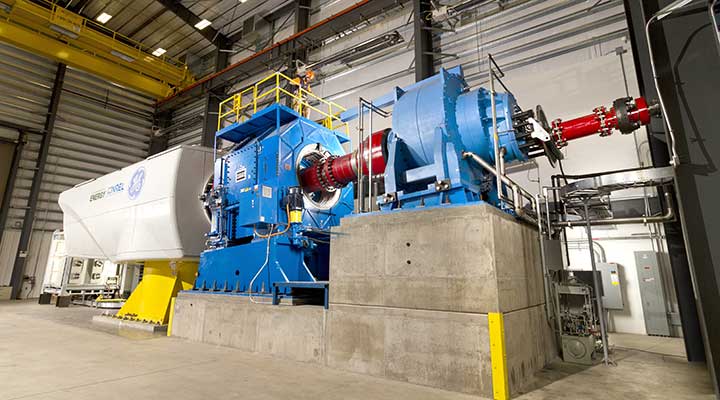
5-MW Dynamometer
Useful for offshore wind turbines and future land-based turbines, the 5-MW dynamometer features an 8,000-hp AC induction motor with a variable-frequency drive and 480 V, 690 V, and 13,200 V AC grid connections.
See the Dynamometer Specifications at the National Wind Technology Center for more details about each dynamometer.
Data Acquisition and Results
NREL researchers can emulate rotor, tower, pitch, and yaw systems with computer simulations operating in real time. We work with our partners to:
- Perform steady-state research validation to determine a drivetrain's "power curve," or how its electrical production relates to the mechanical energy input
- Conduct highly accelerated life research validation, intentionally overloading the drivetrain to help determine its useful operating lifetime
- Employ "model-in-the-loop" techniques to emulate rotor, tower, pitch, and yaw systems with computer simulations operating in real time
- Apply secondary forces and moments other than the primary, driving torque or force
- Connect to the controllable grid interface to provide a better understanding of how drivetrains react to grid disturbances.
Partner with Us
The Flatirons Campus includes experimental laboratories, computer facilities for analytical work, tools and machine shops, office space for industry researchers, and space for assembling components and systems.
NREL offers a variety of ways for organizations to gain access to our wind technology expertise:
- Partner with us through technology partnership agreements.
- Participate in subcontracted wind research through solicitations and requests for proposals.
- Use our cutting-edge research facilities to develop and evaluate wind technologies.
Learn more about working with NREL.
Learn about NREL’s other wind energy facilities.
Share
Last Updated Feb. 18, 2025