NREL Collaboration Could Realize Significant Energy Savings for Farm Tractors
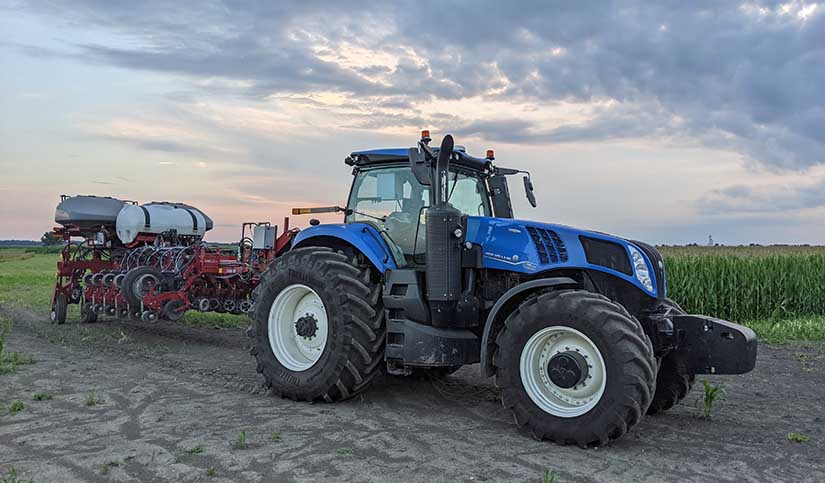
Decades ago, the invention of the diesel combustion engine revolutionized the agricultural industry. Diesel farm tractors were faster, more powerful, and more durable than their gasoline-powered predecessors and allowed farmers to grow more food using less fuel.
Now, a collaboration between the National Renewable Energy Laboratory (NREL) and Purdue University is poised to offer another technological leap forward: a new hydraulic system, equipped with novel controls, that can heighten the hydraulic efficiency of a farm tractor by 50%.
Novel Hydraulic System Applies the Right Pressure
The majority of farm tractors in the United States use a hydraulic system. This system operates much like a human heart: Hydraulic pumps create a “heartbeat,” pumping fluid into the tractor’s “veins” to build the pressure needed to move cylinders and pistons. Those cylinders and pistons allow tractors to plow fields, plant seeds, and fertilize the soil.
But there is a catch to most modern tractors: They can only pump hydraulic fluid at a single pressure. In reality, each component—responsible for plowing, planting, or watering—needs a different pressure to operate. The system has to “throttle” back the pressure to supply only the amount of actuation each component needs.
Unfortunately, throttling is highly inefficient. Some cutting-edge tractor designs are only capable of using 20% of the energy they produce.
“Every time you throttle the pressure within a tractor hydraulic system, it’s a lost opportunity,” said Saad Akhtar, a commercial vehicles researcher who helped lead the NREL/Purdue collaboration. “And those losses add up over the lifetime of the tractor.”
In response, researchers at Purdue University developed a state-of-the-art multipressure rail system that can provide three different levels of hydraulic pressure to a tractor component.
Now, after a five-year collaboration, NREL researchers have created an innovative controller system, designed to be installed onboard tractors, that can precisely calibrate the hydraulic pressure that reaches each component. Even better, it is equipped with a machine learning system that allows it to adjust its operations in real time for maximum efficiency.
Combined, the multipressure hydraulic system and NREL’s onboard controller could allow farm tractors to harness 50% more hydraulic efficiency. In other words, it significantly increases the amount of hydraulic energy converted to useful work, which can be used to run the tractor’s auxiliary functions—the fertilizer pump, vacuum and bulk fill fans, and other components. It can also create fuel savings of nearly 10%.
According to Andrea Vacca, director of Purdue University’s Maha Fluid Power Research Center, the pressure control system developed for the project “has never been attempted in agricultural vehicles.”
“Given the amount of fuel that a typical tractor consumes, this is a massive improvement,” Vacca said. “And this is only the beginning.”
New Controller System Harnesses Hydraulic Efficiency
The controls system was built using two features, Akhtar said: a “state-space representation”—or a mathematical model of the hydraulic system—and “deep reinforcement learning”—a kind of artificial intelligence that teaches a machine to achieve a specific goal by either penalizing or rewarding its behaviors.
The NREL research team, composed of Eric Miller, a commercial vehicle technologies researcher; Andrew Glaws, a computational scientist; and Akhtar, first built a mathematical model of the hydraulic system that could simulate a tractor’s actual operations. Then, they built a supervisory controller programmed to earn a reward when it minimized the hydraulic system’s energy losses or take a penalty when it failed. In this way, the system can learn, in real time, to optimize a tractor’s energy efficiency, no matter what its operating conditions.
The energy and fuel savings created by the NREL/Purdue collaboration could present a significant opportunity for the agriculture industry, which produces roughly a quarter of the world’s greenhouse gas emissions. Farm equipment, like tractors and combines, are not natural fits for today’s shift to zero-emissions technologies. These heavy machines can operate nearly continuously during a growing season and are often parked in the field overnight. Their intense operations present fewer opportunities to recharge than, say, an electric bus or truck, which often returns to the same place each night.
Reducing the fuel consumption of these diesel vehicles and increasing their hydraulic efficiency, Akhtar said, presents an immediate opportunity to reduce the sector’s harmful emissions without compromising their service or productivity.
“Imagine that 30 to 40% of the United States’ tractors suddenly operate with 10% less fuel and a lot more hydraulic efficiency,” Akhtar said. “When you consider the size of the U.S. agricultural sector, the impact scales up very quickly.”
NREL’s Control Framework Could Go Beyond the Farm to New Frontiers
The novel controls framework NREL developed is not just limited to farm tractors. It has applications in nearly every off-road sector—from freight rail to marine vessels and aviation.
“The deep reinforcement learning aspect of our controls framework could be a great way to optimize the control strategies for hybrid-electric, battery-electric, and even hydrogen powertrains,” Akhtar said. “We make a lot of cutting-edge vehicle models at NREL that just need to be connected to the framework. From there, we define the rewards function, and we’re ready for optimization.”
In other words, the potential for energy savings extends far beyond the farm—and is ready to expand to new frontiers.
Learn more about NREL's sustainable transportation and mobility research and its specific focus on advanced commercial vehicles. And sign up for NREL's quarterly transportation and mobility research newsletter, Sustainable Mobility Matters, to stay current on the latest news.